The complete history of 3D printing
Find out about where 3D printing started and how it became the exciting technology and industry it is today.
While 3D printing is a relatively new technology, its history is deep, varied, and interesting – and, of course, still evolving. Here, we’ll take a brief look at the origins of the technology, its rise in popularity, and use, and what we believe the future holds for it.
Early 3D printing
The first 3D printers
The earliest 3D printer originated in 1981, when Dr. Hideo Kodama invented one of the first rapid prototyping machines that created parts layer by layer, using a resin that could be polymerized by UV light. In 1986, the first patent for stereolithography (SLA) was filed by Chuck Hull, who is considered “the inventor of 3D printing” for creating and commercializing both SLA and the .stl format – the most common file type used for 3D printing.
In 1988, Carl Deckard, a student at the University of Texas, licensed selective laser sintering (SLS) technology – another type of 3D printing that uses a laser to sinter powdered material into solid structures. Shortly after, in 1989, Scott Crump patented fused deposition modeling (FDM) – also known as fused filament fabrication (FFF) – and founded Stratasys, one of the main players in the 3D printing industry to this day. That same year, Hull’s company, 3D Systems Corporation, released the SLA-1 3D printer.
The 1990s – and the growth of the 3D printing industry
The 1990s saw a great deal of growth for the early 3D printing industry, with new companies founded and new additive manufacturing technologies being explored. It wasn’t until 2006, however, that the first SLS printer became commercially available.
The RepRap Project
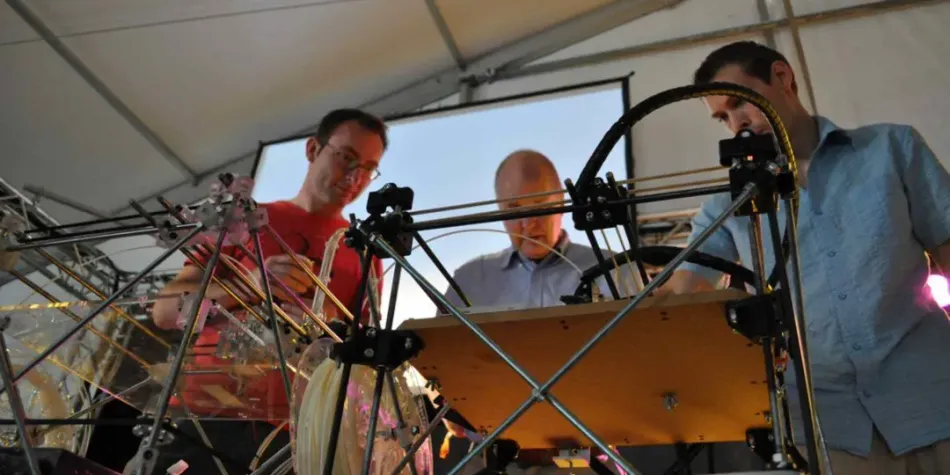
2005 proved to be a landmark year for 3D printing technology, thanks to the rise of an open-source initiative called the RepRap Project, founded by Dr. Adrian Bowyer.
The initial goal of the project was to re-think additive manufacturing, starting with FDM/FFF, as a low-cost technology capable of self-replication. The result was a 3D printer called the RepRap, which became an inspiration for essentially every successful low-cost 3D printer from that point on.
The RepRap 3D printer is made of many plastic parts that can be printed by the RepRap itself. This means that any owner of a RepRap can print another 3D printer – hence “self-replicating” – along with other parts, tools, or designs.
The 2000s – open-source opens doors
Because it is open-source, thus making 3D printing technology accessible to virtually anyone with a computer, the RepRap was named the number-one “most significant 3D printed thing” by 3Dprint.com in 2017.
The success of the RepRap project was a catalyst for the rise of commercial 3D printers. Many of the patents filed in the 1980s regarding FDM also entered the public domain in 2006. This caused an even larger surge of 3D printing manufacturers into the market – one notable example being Makerbot, which was founded in 2009. Makerbot was a large force behind bringing 3D printing into the mainstream market, and opening the door for both professional and amateur users, or “makers.” The company sold open-source DIY kits that enabled customers to build their own 3D printers. Its online file repository, Thingiverse, also houses hundreds of thousands of free and paid downloadable 3D printing files. The site soon became the largest online community for 3D printing in the world.
The founding of Ultimaker
Ultimaker grew out of the Protospace FabLab in Utrecht, the Netherlands, in 2011. It started as a project between a few friends trying to make a 3D printer that would deliver accurate, useful parts without the costs and hassle that comes with larger industrial additive machines.
The inspiration for this came from the RepRap project. After many evenings spent building this “replicating rapid prototyper” – an open-source machine that could replicate most of its own components – they had a working 3D printer. But they noticed how much time and constant maintenance was required to keep it functioning properly, and began investigating design improvements that would make it even better. Over time, Ultimaker evolved, from DIY kits to a full ecosystem providing hardware, software, and materials fit for industrial environments.
3D printing today
Since the rise of commercial 3D printers, the landscape of the industry has changed quite drastically. Now, 3D printers – both desktop and otherwise – are used in industries and sections such as aerospace, architecture, manufacturing, automotive, healthcare, construction – and, of course, many more.
Examples of modern-day 3D printing
In 2018, for example, the International Space Station printed the first tool in space, using a low-gravity 3D printer. This enabled workers to access the tools they needed for maintenance far more quickly, rather than waiting for them to be delivered from Earth.
3D printing technology also enables organizations like Gerhard Schubert GmbH to transform the ways in which they operate, creating "digital warehouses" of parts and tools that can be printed on-demand by both manufacturing organizations themselves, as well as their customers.
3D printing materials of today
Additionally, manufacturers can make use of an ever-growing stable of 3D printing materials, which enable the creation of parts that are heat and chemical-resistant, flame-retardant, ESD-safe, and made of metal, carbon fiber, glass fiber, and more. In 2015, Swedish company Cellink brought “bio-ink” to market, a seaweed-based material that can be used to print biological tissue – and potentially human organs. This is one of many use cases that 3D printing companies believe they can use to revolutionize various industries. This means the future of 3D printing holds a great deal of potential – a potential we’re excited to see realized.
The future of 3D printing
Exactly what the future holds for 3D printing is fairly speculative, but adoption of consumer 3D printers will likely continue to accelerate. This will change the way the average person acquires goods, placing the means of manufacturing into their hands, whether they are printing prototypes, tools, or end-use parts. The technology’s acceleration will also serve to decentralize manufacturing as a whole – preventing supply chain issues, decreasing transportation and shipping costs, and drastically decreasing both time and money spent on acquiring goods.
The materials used in 3D printing will also continue to expand and evolve. The rise of printing metal, for example, is already unlocking applications and use cases previously thought impossible to achieve in ways other than traditional manufacturing methods. The use of metal in 3D printing will potentially see organizations using 3D printers for the serial production of metal parts – producing them faster and more cheaply than ever before.
3D printing by the (future) numbers
Other predictions focus on broader uses of 3D printing. In 2020, 3D printed molds and tools were valued at $5.2 billion – a number that is expected to grow to $21 billion by 2030. End-use parts, meanwhile, will increase in value seven times over, to $19 billion, by the same year. Such growth would mean even further transformation of the manufacturing industry, with organizations increasingly turning to in-house manufacturing rather than outsourcing.