The Indy Autonomous Challenge
A high-speed autonomous vehicle race at the famous Indianapolis Motor Speedway. University teams program and race a modified Dallara AV-21 racecar to win $1.5 million in prize money.
Image Credit: IAC/Ansys
The Indy Autonomous Challenge (IAC) will culminate in a final race held in October of 2021, where teams will compete by developing software that will drive a modified Dallara-built Indy Lights race car around the Indianapolis Motor Speedway (IMS). The challenge began in late 2019 as teams formulated their plan, demonstrated their ability to program an autonomous vehicle, and have recently taken part in hackathons. This article will cover the impetus of the competition, the technical specifications, the simulation tools, and why this competition matters.
A Rich Racing Heritage
In decades past, grassroots racing had one purpose: to showcase automotive technology. The old adage, “Win on Sunday, sell on Monday'' drove manufacturers to develop faster, better-handling cars. Technology transfer was a seamless thing; the racecars were showroom stock, and what you watched at the track is what you could buy and drive yourself. The technology seen in F1, Indy, or even Le Mans seems to continue to deviate from road car technology. But in the case of autonomous vehicles, the same code used to race a Dallara around IMS could be used to develop the code for autonomous passenger cars.
The Indy Autonomous Challenge seeks to help overcome prominent barriers to automated vehicle (AV) commercialization through an intensive learning cycle where the next generation of automotive engineers can test the boundaries of current assumptions. Here’s how.
The Indy Autonomous Challenge Race Specifications
1. The Car: A Modified Dallara-produced AV-21 .
Dallara Indy Light Chassis
The Clemson University International Center for Automotive Research (CU-ICAR) is converting an AV-21 Dallara to accept the autonomous algorithms from each university team in the IAC. To keep everyone apprised of the mods, there are monthly virtual design reviews. To start, here’s what an AV-21 brings to the table:
Dallara AV-21 Specifications
Chassis | Carbon |
Race weight | 640 - 649 kg (including fuel and driver) |
Powerplant | AER P63 2.0L turbocharged 4-cylinder |
Horsepower | 450 (+50 for Push-to-Pass) |
Gearbox | Ricardo 6-speed semi-automatic (paddle shifters) |
Clutch | Tilton carbon 3-plate design |
Suspension | Double wishbone |
Dampers | Dynamic Suspension’s (Multimatic) DSSVs |
Fuel | VP Race Fuel |
Wheels | Motegi Racing aluminum 15-inch rims |
Tires | Cooper/IndyLights branded slicks and rains |
Electronics | Cosworth looms, data logger, dash and sensors, Life Racing ECU, drive-by-wire throttle control, driver-adjustable map |
Aerodynamics | Adjustable flaps on the front and rear wings |
After CU-ICAR worked their magic on the Dallara, additional Lidar, radar, and optical cameras were added as well as additional batteries which are needed to power the added wiring and sensors. Internal cooling was also added for the batteries and electronics.
2. The Proving Ground: Virtual and Real Speedways
In addition to three on-track test sessions, trials of the autonomous software on a virtual representation of IMS will also be conducted in a VR driving simulator. The VRXPERIENCE Driving Simulator from Ansys includes scanned tracks, like Mcity at the University of Michigan. That track is used for ADAS testing, and by having the real-world track for physical testing side-by-side with the simulation, engineers can easily conduct validation and benchmark testing.
The Ansys simulator also has the ability to take the raw scanned track data (a point cloud collected by specialized companies) and convert it into a high-fidelity model. Often, this process is arduous and takes simulation engineers weeks to define and trim surfaces for simulation. Having that capability within the simulation suite is a huge time-saver on the path to virtual testing.
The Indy Autonomous Challenge simulation track developed by Ansys. Image Credit: Ansys.
3. The Race Schedule: Five Rounds of Competition
Each round of the competition is a prerequisite to the following one. The five rounds of the competition are as follows:
- Launch, Completed February 28, 2020 – The first stage of the competition comprises the formality of registration and the writing of a specific white paper, which included the team’s background research, details on which simulation software will be used, and a project plan.
- Demonstration, Completed August 19, 2020 – Before getting into racecar engineering, teams are asked to prove that they can program a passenger vehicle to undergo a range of autonomous maneuvers (acceleration, turning, declaration, and a complete stop). Teams either submitted a short video as proof or completed the evGrandPrix Autonomous Series.
- Simulation Race, June 30, 2021 – The university engineering students will upload their own autonomous algorithms to compete in two stages of a simulated race. First, 10 solo laps will demonstrate their ability to control the IL-15 racecar, which must be completed in ≤ 15 minutes. Second, teams will compete head-to-head for 20 laps, must not crash, stay within the track limits, and complete the race within 105% of their matched competition (similar to the 107% rule of F1 qualifying).
- Qualification, October 21-22, 2021 – After a safety and technical inspection, each team must complete 10 laps at IMS in ≤ 15 minutes (average speed ≥ 100 mph), and one of those laps must be completed in ≤ 75 seconds (average speed ≥ 120 mph). The starting grid for the final race is set by the safe completion of the qualification race (in order of the lowest total time for the 10 laps).
- Final Race, October 23, 2021 – The winner will be determined in a 20 lap race at IMS, with an average speed ≥ 120 mph, completed in ≤ 25 minutes. Tech inspection will take place prior to the race, and teams may be disqualified for any rule breaches, impeding another racecar on the track, or cheating. The winner receives $1 million USD, second place receives $250,000, and the third spot will be given $50,000.
4. The Engineering Toolkit: Design, Simulation, and Track Testing
To prepare for the simulation race, teams will have access to the Ansys VRXPERIENCE Driving Simulator, which uses SCANeR and the SCADE Suite. The simulator will reside on Microsoft Azure, which teams may already be familiar with using for cloud computing.
Ansys hosted four hackathons for the teams to compete in and gain experience in the lead-up to the simulation race. Teams will train their AI (artificial intelligence) software within the programmable logic controller through numerous different driving scenarios.
The simulator itself contains a host of modules that could be used both for passenger car and racecar engineering, including driver-in-the-loop simulations (to get the human/passenger feedback), hardware-in-the-loop simulations (to test out ECUs), and model-in-the-loop testing, where multiple driving scenarios can test separate vehicle dynamics or autonomous parameters.
Engineers Deploy Advanced Simulation Techniques to Design Autonomous Vehicles
In addition to the VR driving simulator discussed above, many simulation tools are used to design autonomous (and traditional) vehicles. The AI used to drive an autonomous vehicle needs to be trained in a large number of driving situations. And while there are private proving grounds where these vehicles are tested in real life, there’s simply not enough time to gather data and train the AI in the real world. The majority of the training and testing is done virtually, and then physical testing takes place, in a sense, as a validation of the simulation.
Engineers in motorsport and automotive engineering use simulation daily. Nearly every discipline with automotive design has a specialized simulation tool to help them design and optimize a car. Structural engineers use FEA and forming simulations, aerodynamicists use CFD, both for full-vehicle performance and individual components or internal flow systems, such as cooling and engine air inlets, and vehicle dynamicists use kinematic analysis tools and the same driver-in-the-loop simulations described above.
By limiting the physical prototyping and testing required, design timelines can be significantly shortened. But it’s also important to note that these tools increase sustainability. In the push for limiting climate change to just 2°, the transportation segment must play a large role, as it currently produces nearly a quarter of the world’s CO2 emissions. And simulation is just one of the many engineering tools that will be used to improve sustainability in the automotive industry.
For example, in the realm of motorsport aerodynamics, the full-scale rolling-road Windshear wind tunnel in North Carolina requires its own power station to test a vehicle at speeds of up to 150 mph. Add to that the emissions of flying the engineering team to the wind tunnel for a three-day test, and the environmental impacts are not insubstantial. If the same vehicle were tested in CFD, using cloud computing resources and even open-source software (like OpenFOAM), the energy and costs required to reach the same conclusions are minuscule in comparison. There’s no separate power grid required, no flights, and no consumables (coated tires, adjustable ride height system for the wind tunnel, and a suite of real parts to test).
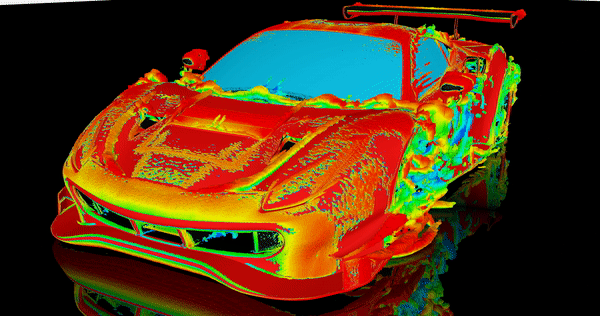
The added bonus of simulation tools (versus IRL testing) is the ability to dive into the results and dissect the findings. Post-processing simulations and spending the time to visualize results are two of the incredibly powerful facets of all simulation tools. VR driving simulators allow you to go back into scenarios and determine where things went off the rails and where things improved. Similarly, a CFD simulation allows you to see exactly where a design change impacted the pressure signature of the underfloor of a racecar, but a wind tunnel test just reports your overall forces and balance.
Why the Indy Autonomous Challenge Matters
Simulation and autonomous vehicles are a part of the drive towards more sustainable technology within automotive engineering. Simulation reduces physical testing, which decreases emissions, both in terms of vehicle emissions at track tests and in terms of energy consumption when manufacturing and testing components. The IAC is the launchpad for engineers to get familiar with new technology and be a part of the changing landscape toward sustainable transportation.
The challenge is preparing engineers for jobs in autonomous vehicle development. The university engineering students are solving real-life engineering problems, including “edge case” scenarios, which occur at an extreme operating parameter; for example, avoiding unanticipated obstacles at high speeds while maintaining vehicular control. The IAC will allow for testing of safety and evasive maneuvers during the simulation and final races, which will bring more awareness to the public and foster trust in emerging sustainable technologies.
Follow the Indy Autonomous Challenge with Wevolver
Over the following weeks, we will do a deep dive into the IAC, highlighting the vehicle, the teams, and the technologies that make it all possible. Our next article will focus on the simulation race taking place on June 30th, where teams compete to win cash prizes totaling $150,000. We’ll explore what the teams will need to prepare, what they will be testing during the race, and why simulation racing is a crucial part of autonomous vehicle innovation.
In the final IAC event, you’ll see whether Dallara race cars running at over 100 mph can successfully complete a race at IMS without any drivers. The stakes are high, as university teams fight it out for the top prize, but the excitement for the engineering community will also be huge as we watch a high-speed demonstration of autonomous driving.
This article was written by former motorsport engineer Kattie Thorndyke with editing by the Wevolver Team and Ansys Global Industry Director, Tarun Tejpal.
About the sponsor: Ansys
Ansys provides engineering simulation software used to predict how product designs will behave in real-world environments. Founded in 1970, Ansys employs more than 4,400 professionals, many of whom are expert M.S. and Ph.D.-level engineers in finite element analysis, computational fluid dynamics, electronics, semiconductors, embedded software, and design optimization.