Fast Curing Concrete for 3D Printed Construction
Let's take a look at some of the Material Science and Rheology behind 3D printed concrete. This type of concrete is unique because it needs to be strong enough to support the next layer being printed on top.
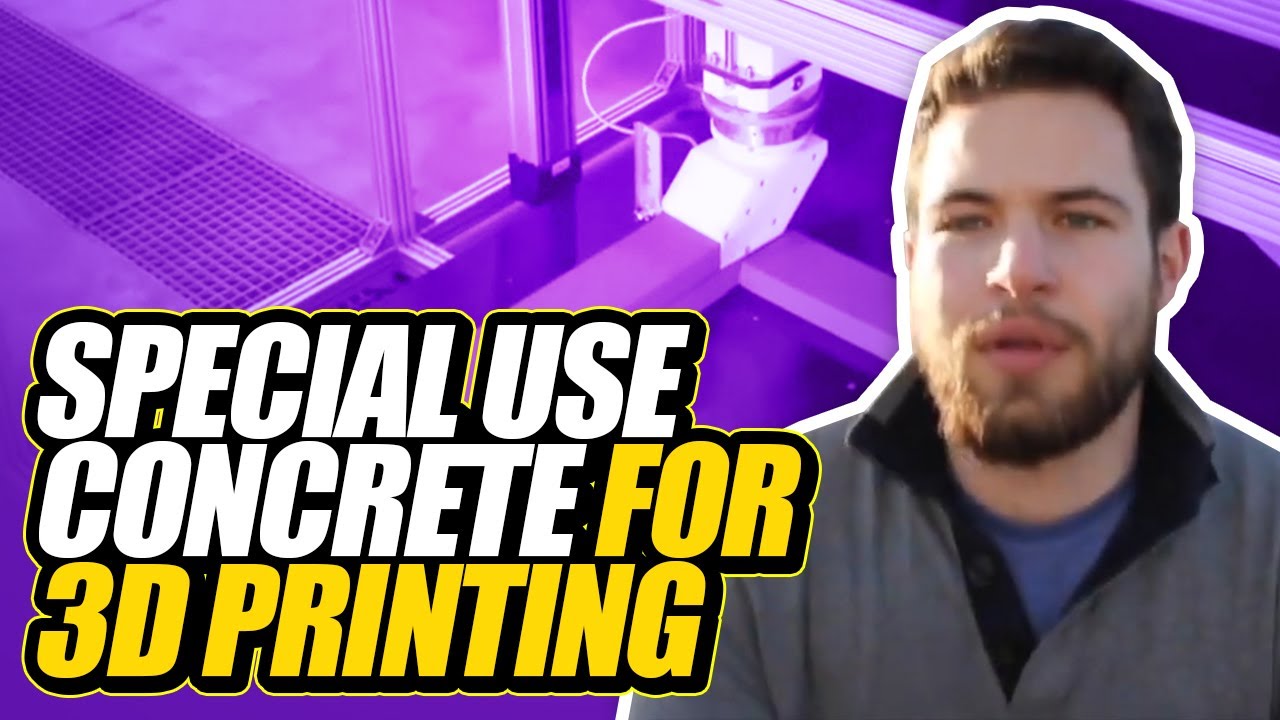
This article was first published on
automate.constructionYou've seen 3D Printed Helmets and 3D Printed Body Parts, but what about 3D Printed Concrete?
3D printed construction might be the most promising way to automate construction so recently many people have been pursuing the perfect mix for printing. Rheology is the study of how materials flow so that is the science being applied to concrete made for printing.
My name is Jarett Gross and I’ve gathered this information mostly from research featured at Digital Concrete 2020 to simplify some of the material science behind forward thinking disruptive construction methods.
These materials range from nearly free adobe mixtures of dirt and straw to ultra strong and highly engineered custom concrete hybrid mixtures that can be cost prohibitive in respect to affordable housing.
Currently most groups automating large forms are using unique mixtures of concrete engineered to have properties conducive to a sturdy structure.
The material needs to hold immediately exiting the machine. Generally that is either achieved by a stiff mortar or a thinner mix with an accelerant added at the point of extrusion to cure the concrete faster and achieve angles gravity otherwise would not permit. (1)
Thixopotry is a property that allows a mixture to flow when it is being moved but remain firm after it has been placed so this is behind many of the developments in this space.
Some of these mixes include various forms of supports which I will cover in an upcoming video, others are strong enough to support themselves like the project in Brazil by InovaHouse3D.
Many mixtures have been considered using Portland cement. Wollastonite micro fibers have been shown to enhance flexural strength without detriment to compressive strength. The same study shows printed concrete demonstrates anisotropic behavior, in other words like the grain of wood it fails easier parallel to the grain vs perpendicular to the grain (2)
Mixes can be thick or have more flow, these properties can be influenced by viscosity modifying admixtures’VMA’. NanoClay can improve the strength of the print but makes the mixture more susceptible to clogging to viscosity modifying admixtures can improve the flow. (3)
Two minute delay time between layers has 25-86% higher strength than a 15 minute interval it is important to get a monolithic structure (4)
Fly ash silica fume metakaolin limestone powder and quartz powder have been identified as having useful properties for printed concrete. Plasticizers, accelerators, retarders, and viscosity modifying agents can be used but increase cost dramatically (5)
Limestone can be implemented with less cement to decrease cost to print and improve sustainability.
Under a 25% replacement rate of limestone powder to cement, the impact on strength is within reasonable limits. (6)
Metakaolin leads to a more dry mix that is stronger after extrusion but more difficult to extrude. Fly Ash can be included to improve the printability. Adding polypropylene fibers was shown to increase the yeild stress. (7)
Here are the details from a mix made in a region where dune sand is an abundant resource (8)
- Cement was replaced by up to 10% silica fume and 30% fly ash
- water-to-binder ratio used in the mix ranged between 0.35 and 0.40.
- superplasticizer was added in the range of 1 to 3%, by binder mass.
- compressive strength increased by 3% when 20% dune sand was utilized, but decreased by an average of 3% for every additional 10% subsequently.
- superplasticizer and higher water- to-binder ratio exhibited improved workability
- replacing cement with silica fume and fly ash, the slump flow and pumpability increased
- Compressive strength increased by an average of 4% for every 10% fly ash replacement. The incorporation of 10% silica fume improved the strength by an additional 14%
Lightweight foam concrete is common but to use it for 3d printing it would need to be extrudable. Extrudable lightweight foam concrete could be great for 3d printing because of its thermal insulation and accoustic qualities in addition to fireproofing.
The target dry density was 800kg/m^3 because that was figured to be the best balance between strength and staying lightweight. (9)
Structural fibers had a negligible effect on the mixes strength in tension, it is theorized that the fresh state properties of the material prevent the fibers to anchor in place which prevents tension strength (10)
As I mentioned, I will soon do a video on the support methods used for this type of construction. Another video on commercially available mixes for printed construction will probably be 3-6 months away as there are many solutions still in development that I would like to include.
Citations
(1) Enhancing Buildability of 3D Printable Concrete by Spraying of Accelerating Admixture on Surface
Shantanu Bhattacherjee and Manu Santhanam Department of Civil Engineering, IIT Madras, Chennai 600036, India
ce17d700@smail.iitm.ac.in, manusanthanam@gmail.com
(2) Effect of Wollastonite Micro-Fiber Addition on Properties of 3D-Printable ‘Just-Add- Water’ Geopolymers
Shin Hau Bong, Behzad Nematollahi, Arun R. Arunothayan, Ming Xia, and Jay Sanjayan
Centre for Smart Infrastructure and Digital Construction, Faculty of Science, Engineering and Technology, Swinburne University of Technology, Melbourne, VIC, Australia bnematollahi@swin.edu.au
(3) Use of the Chemical and Mineral Admixtures to Tailor the Rheology and the Green Strength of 3D Printing Cementitious Mixtures
Mohammad Amin Moeini, Masoud Hosseinpoor, and Ammar Yahia
Department of Civil and Building Engineering,
Université de Sherbrooke, Sherbrooke, Canada Mohammad.Amin.Moeini@USherbrooke.Ca
(4) Characterising Concrete Mixes for 3D Printing
Atteyeh S. Natanzi and Ciaran McNally
School of Civil Engineering, University College Dublin (UCD), Dublin, Ireland
Atteyeh.natanzi@ucd.ie
(5) Rheology Evaluation of Cement Paste with Nanoclays, Nanosilica and Polymeric Admixtures for Digital Fabrication
Hugo Varela, Gonzalo Barluenga, and Irene Palomar Department of Architecture, University of Alcala, Madrid, Spain
hugo.varela@edu.uah.es
(6) Effect of Limestone Powder Substitution on Fresh and Hardened Properties of 3D Printable Mortar
Yaxin Tao, Karel Lesage1, Kim Van Tittelboom1, Yong Yuan2, and Geert De Schutter1
1 Ghent University, Ghent, Belgium
Yaxin.Tao@UGent.be
2 Tongji University, Shanghai, China
(7) Effect of Metakaolin, Fly Ash
and Polypropylene Fibres on Fresh and Rheological Properties of 3D Printing Based Cement Materials
M. Dedenis1, M. Sonebi1, S. Amziane2, A. Perrot3, and G. Amato1
1 School of Natural Build Environment, Queen’s University of Belfast, Belfast, UK
m.sonebi@qub.ac.uk
Université Blaise Pascal, Polytech Clermont-Ferrand, 63174 Aubière, France 3 Univ. Bretagne-Sud, UMR CNRS 6027, IRDL, 56100 Lorient, France
(8) Fresh and Hardened Properties of 3D-Printed Concrete Made with Dune Sand
Hilal El-Hassan , Fady Alnajjar , Hamad Al Jassmi, and Waleed Ahmed
United Arab Emirates University, Al Ain, UAE
helhassan@uaeu.ac.ae
(9) Investigation on the Rheological Behavior of Lightweight Foamed Concrete for 3D Printing Applications
Devid Falliano1, Giuseppe Crupi2, Dario De Domenico2, Giuseppe Ricciardi2, Luciana Restuccia1, Giuseppe Ferro1, and Ernesto Gugliandolo3
1 Polytechnic of Turin, Turin, Italy
devid.falliano@polito.it
2 University of Messina, Messina, Italy 3 G. Gugliandolo s.r.l., Messina, Italy
(10) Experimental Investigation on the Early Age Tensile Strength of Fiber Reinforced Mortar Used in 3D Concrete Printing
Marta Fioretti1, K. Sriram Kompella1, Francesco Lo Monte1, Laura Esposito2, Costantino Menna2, Sandro Moro3, Domenico Asprone2, and Liberato Ferrara1
Department of Civil and Environmental Engineering, Politecnico di Milano, Milan, Italy
2 Department of Structures for Engineering and Architecture, Università degli Studi di Napoli Federico II, Naples, Italy laura.esposito2@unina.it
3 BASF Construction Chemicals Italia, Treviso, Italy