Festo BionicSoftArm
Whether free and flexible movements or defined sequences, the modular pneumatic lightweight robot can be used for a wide variety of applications in the context of human–robot collaboration depending on the composition and mounted gripper.
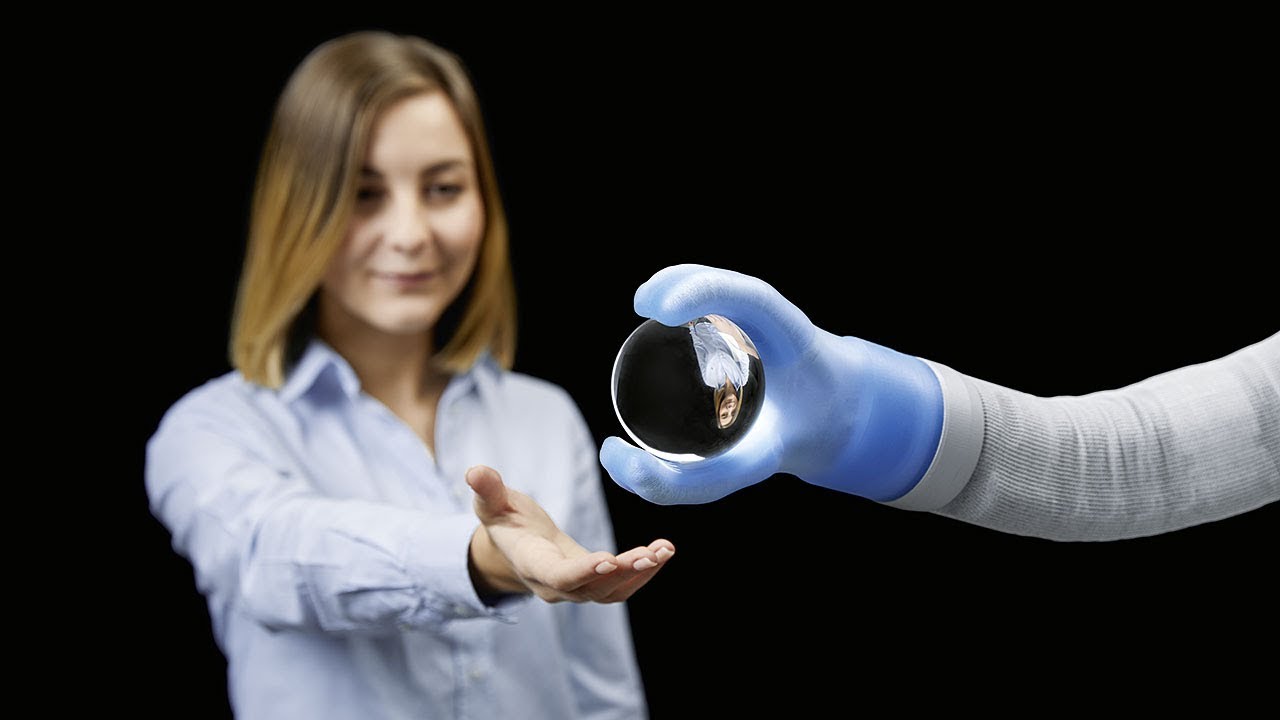
Potential for the collaborative workspaces of the future
Invented by the company Festo, the BionicSoftArm is a modular robotic arm with numerous potential applications. The video begins by showing its previous prototypes starting with the 2010 version of a robotic metal arm with simple grippers followed by the 2017 version of a covered cylindrical arm with more flexibility in its design. In 2019, the company debuted the latest version of the robotic arm with 7 degrees of freedom which allows more elasticity to its movements. This is made possible by a pneumatic bellow segment, and pneumatic rotary drive. Its appearance has segmented bellows with a knitted fabric combined with other installed components in the color of blue and white.
The BionicSoftArm interface allows for different types of grippers, the first being the BionicSoftHand that is modeled after the human hand. This mechanism is also a patented invention by Festo. The next gripper is a clamp-like device that can hold and release various types of objects. And the last type of gripper uses an adaptive type of suction to transport objects such as small metal balls to another location. It also demonstrates how the robotic arm can detect and move around obstacles in a smooth transition between locations.
As a result, the BionicSoftArm meets two essential requirements for tomorrow’s collaborative workspaces, increasingly eliminating the strict separation between the worker’s manual tasks and the automated actions of the robot. This means that in the future, both humans and machines will be able to work on the same workpiece or component at the same time.
To achieve this, it means that on the one hand, automated robot solutions must be able to interact with humans directly and safely – without the two having to be isolated from each other for safety reasons. On the other hand, such open workspaces will primarily demand robots that can be easily customized and independently adapt to different products and scenarios