Our latest report, Building the Factory of Tomorrow, offers an in-depth analysis of the core forces shaping modern industrial production, from the accelerated pace of technological innovation to the integration of human-robot collaboration in next-generation factories.
Download this detailed report to explore:
- Cutting-edge advancements in AI, Quantum Computing, and Hyper Automation that are impacting manufacturing processes.
- The impact of globalized supply chains and virtual collaboration tools in enabling seamless cross-border operations.
- The shift toward sustainable production models, emphasizing circular value chains and carbon-neutral practices.
This report provides valuable technical insights for engineers, industry leaders, and decision-makers seeking to leverage the latest innovations and strategic trends to enhance operational efficiency and remain competitive in a rapidly changing landscape.
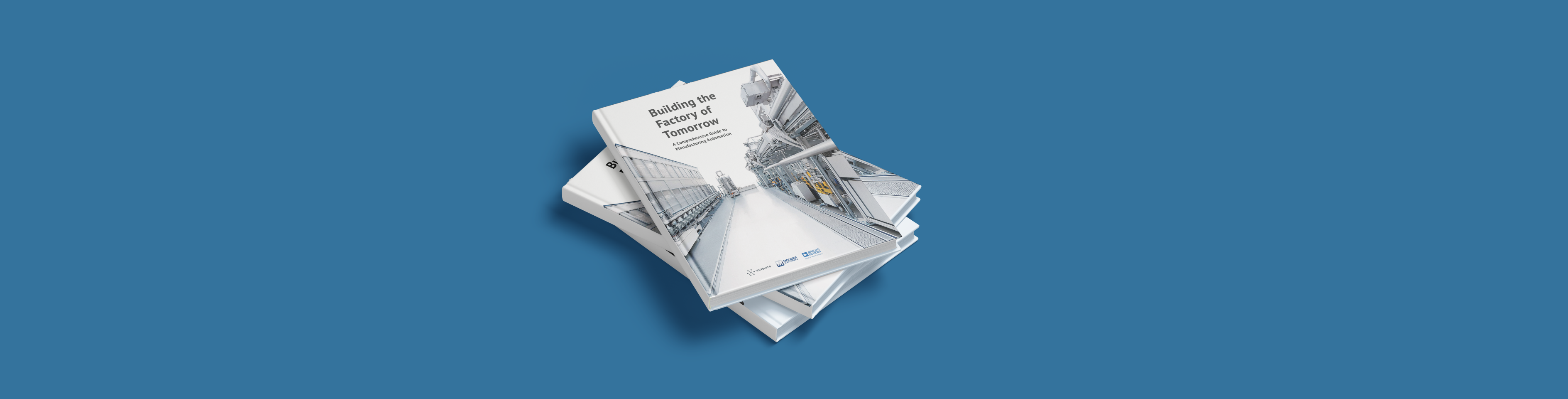
The introduction of smart technology into the factory environment is unlikely to be a continuous process. In previous chapters, we have discussed the options available to operators when considering how to integrate smart technologies into existing processes, along with the possibility of building a new facility from a brand new, greenfield site.
However, when considering the introduction of smart technologies in the real-world, the pace with which new processes can be adopted will be limited by the investment required and the possible need to comply with regulations. As a result, it is highly likely that operators will integrate new equipment in phases. The factory of the future will therefore evolve over time as each innovation is introduced.
The goal of smart technology is to integrate all the different activities that contribute to the output of a system. The example of the smart factory sees supply chain, production, maintenance, and scheduling all integrated into a single entity. In a traditional factory, all these activities would have been conducted separately. In the new model, data is collected from sensors at every step of the process and shared with the whole network to help make decisions. In this way, the supply chain can ensure that raw materials are provided to the production line at the right time, and logistics can plan to provide transport for the finished goods just as they become ready.
Example of a flexible production line layout.
Flexible Production Lines
A traditional factory might house many machines, each performing a single task. Industry 4.0 connects these machines into a network that works as several layers. The bottom layers are responsible for the function of the machines themselves, whereas the middle levels are responsible for the control of the whole factory floor. At the highest or enterprise level, operations are integrated into the software that runs the entire organisation. This level brings together not just the management of production, but also the supply chain, maintenance, and logistic aspects of the operation.
This networking of the different levels allows information to be shared up and down the organisation. From ensuring that raw materials are where they are needed to collecting data that will help with the maintenance burden of the factory, it is this sharing of data that defines Industry 4.0.
The benefits of these innovations can be seen in several areas. The ability to plan and control production closely allows the manufacturer to work more efficiently. Using the data collected, manufacturers can keep close control of the delivery of raw materials to the factory floor, reducing costs and logistical requirements. Data can also be used to reduce disruption caused by machine breakdowns by identifying problems before they become significant.
However, possibly the biggest benefit of Industry 4.0 is increased agility and flexibility. The integration of all levels of the factory allows the manufacturer to respond to current demands and trends much more quickly than traditional methods would allow.
The responsiveness of such a factory creates new problems for product designers. As factories become quicker to respond to demand, consumers will become accustomed to rapid service. The manufacturer will be under pressure to improve their time to market. Suppliers that can develop and deliver new products rapidly will be best placed to reap the benefits that Industry 4.0 can provide.
The result is that, just as the manufacturing process becomes quicker, the design process will need to be equally responsive. Tools and services that allow engineers to design the next generation of their products rapidly will allow their company to take full advantage of the Industry 4.0 revolution.
Condition-based Monitoring - Predictive Maintenance
Industry 4.0 changes the methods that operators use to ensure the safe running of their facilities. By installing a range of sensors on every machine and connecting them together, operators can collect a huge amount of data in real-time. This is then collected, but the key task is to analyze this data in a useful way. This is the task of the digital twin. A digital twin is a replica of the real device that exists electronically in a virtual space. It is a model of the original machine that mimics how the real-world example should operate.
However, a digital twin that existed purely as a replica would be of limited use. If the only role of the digital twin is to predict how a machine should operate, it would not provide much assistance in the real-world. However, by taking all the data collected from sensors within the original and feeding it into the digital twin, it is possible to create a predicted behavior of the machine based on current trends.
This is known as condition-based monitoring (CBM). In CBM, the condition of the device is monitored in real-time by a sensor such as the ADI OtoSense Smart Motor Sensor to decide what maintenance must be performed. In this way, maintenance is only performed when decreasing performance or upcoming failure is detected, in turn minimizing downtime and the cost of parts. Combining the model of the original and comparing it with real-time data from sensors makes it possible to identify and even predict the work required.
An unexpected vibration could indicate damage that will require attention. An increase in power consumption might suggest that parts are nearing the end of their life and need replacing. This contrasts with preventive maintenance in which work is conducted at set periods of time. There is a potential for parts to be replaced before they have reached the end of their life, resulting in unnecessary expense.
As an example, subtle changes in the operating temperature of a machine can provide early warning about potential failures or allow the operator to adjust its operation to make more efficient use of energy. For example, wireless vibration monitoring platforms such as The Analog Devices Voyager 3 can offer continuous, high-resolution vibration analysis through its advanced sensor technology and wireless communication. By providing indications of maintenance requirements before failures occur, the operator can plan work ahead of time and minimise the impact on the production schedule.
In addition, the comparison of historical data with expectations will allow the operator to refine the accuracy of the digital twin. This will allow the digital twin to be even more useful in predicting maintenance or failures in the future. When combined with Product Lifecycle Management (PLM) techniques, operators can use this accuracy to ensure replacement parts are available at the times and places they are most needed, even for facilities that are in remote regions.
The use of predictive maintenance can provide a measurable return on investment. Predictive maintenance will reduce the amount of time that a machine is prevented from operating, and can improve its effectiveness by addressing problems before they affect performance. As a result, the investment required to create a predictive maintenance system will quickly be returned in greater overall equipment efficiency (OEE).
While this report considers the subject of predictive maintenance in the context of factory-based applications, it is important to note that the same techniques can be applied to almost any application. Any industry that utilizes complex or expensive machinery, from agriculture to energy production, will benefit from an advanced predictive maintenance system. This extends beyond machinery. The ability to collect real-time information can even reach into areas such as real estate and civil engineering where predictive maintenance can play a key role in providing peace of mind in safety-critical situations.
Quality Management
On any production line, one of the key tasks is quality control. The sophistication of modern embedded vision systems allows automated, 100% visual inspection. Each item leaving the production line can be imaged by a dedicated camera that uses deep learning to compare dimensions to a standard in real-time. Machine learning is vital to the performance of these vision systems, both to discard faulty products and to understand subtle changes in quality that might indicate deeper problems. Such compact devices rely on edgeAI/TinyML to analyze results with the lowest latency, allowing them to respond quickly to real-time observations.
Smart quality systems do not only have an impact on quality control. The data collected from inspection systems can be fed into the digital twin to identify rising trends in the number of faulty products. This information can be correlated with other data collected from the same machine, including temperatures and energy consumption. By analyzing all the associated data, the maintenance of the machine can be planned before a major failure occurs, which in turn minimizes the disruption to production.
Embedded vision systems like ADI’s ADTF3175 Time-of-Flight Module are continually being developed to make them smaller, more cost-effective, and more capable. Easily connected to existing networks, quality inspections have a key role to play in a wide range of other applications in the smart factory, from logistics to safety.
Sustainable Manufacturing
The circular economy is a goal that many manufacturers are pursuing to reduce their impact on the environment. Although activities such as recycling are a key part of this circular concept, it goes far beyond simply the subject of disposal and looks at the entire product lifecycle.
The smart factory is ideally placed to make a huge impact on sustainable manufacturing. Many processes can employ smart materials designed to optimise the usage of resources, such as helping to improve energy efficiency in manufacturing operations. For instance, thermoelectric materials can convert waste heat into electricity, providing a sustainable way to recover and utilize energy that would otherwise be lost during manufacturing processes.
Other smart materials possess self-healing properties, enabling them to extend their useful lifespans by repairing damage automatically and reducing the need for frequent replacements. Smart materials can even be equipped with sensing capabilities that can be used to monitor environmental conditions, equipment performance, and product quality in real-time. This might take the form of a colour change if a product is subjected to abnormal stresses, information that can be collected using vision systems to further enhance the accuracy of the digital twin.
The smart factory can also deliver huge benefits beyond the manufacturing process. It can encourage the increased use of refurbished equipment. Incorporating smart technology into machines and collecting data on their operation will be key. By understanding how machines fail with the use of real-world data, manufacturers can develop more effective refurbishment programs. This will allow them to refurbish and resell the equipment at a far lower cost in energy and resources when compared to a brand-new unit.
However, this will require manufacturers to change their attitudes towards the ongoing life of their products. In the modern business world, product returns are frequently viewed in a negative light. A product return usually means a quality control issue that needs to be addressed, and most companies use the number of customer returns as a metric for the performance of their manufacturing process.
The circular economy will require both manufacturers and customers to challenge their views. They must be willing to give up the convenience of buying brand new equipment and overcome the concerns created by buying products manufactured from recycled materials. The smart factory will provide the data to overcome these reservations. With data, it is possible that the new goal will be to encourage 100% returns to develop a more sustainable approach to manufacturing.
The Digital Thread
The ability to keep track of components and processes will be vital to developing a circular manufacturing strategy. Traceability describes how every aspect of a component can be recorded. From the original raw materials from which it was made, through the manufacturing processes it followed, to the inspection that was carried out once completed, there needs to be a record of the life of that component.
This traceability will allow users to analyze the performance of components and prevent failures. For example, if the failure of one component can be traced to a flawed manufacturing process, it is possible to identify all other components that used the same process. Records will allow the manufacturer to advise customers that they need to take action to prevent similar failures. Anyone who has received a letter from the manufacturer of a car that needs to be recalled for upgrades has seen traceability in action.
Product recalls in the automotive industry hit the headlines due to the number of vehicles that are affected – sometimes in the hundreds of thousands. However, the same process is used across all sectors of industry, and this generates a huge amount of information. The use of computers has made this information easier to process, sort, and analyze.
It is important to understand that the life of a component does not begin when it is manufactured, nor does it end once it is installed. It is possible to trace the lifespan of any component from the very start of the design process, and this can continue to the very end of its life. Using digital technologies and the power of the smart factory, it is possible to collate this information into a single record. This is what has become known as the Digital Thread.
The digital thread is the record of the component and is woven through every stage of its life like a thread through a fine silk garment. This record then allows an engineer to understand everything about the component and make decisions based on this information.
The digital thread presents benefits to engineers at all stages of the product lifespan. The digital thread can help the product-selection phase of the design process. Having access to all of the information about a component, the designer can select the best solution for any particular design and be confident in their choice. The digital thread will contain data on the materials of the component, ensuring that the design will comply with any environmental or performance restrictions that might apply. Finally, the digital thread will contain information concerning the end of a product’s useful life, and whether the item can be recycled or refurbished to help improve sustainability.
The Human Factor
The smart factory no longer relies on static machines. Robots have been a common sight on many production lines for decades, but recent developments have given them new capabilities. A range of technologies across multiple fields have all matured at the same time to create a new generation of robots that are transforming the factory. At the heart of this new breed of robot is the processing power of modern microelectronics, but they are nothing without the advances in other areas of technology, from wireless connectivity to batteries and motors.
These robots are not self-aware and do not employ true artificial intelligence. However, they are designed to understand the environment around them. Gathering this information, they respond and adapt their actions to accomplish their assigned task. From navigating a busy factory floor to handling sensitive cargo, these robots can act autonomously by employing a form of artificial intelligence known as machine learning.
Moving around the factory floor are Autonomous Mobile Robots (AMR). They have found applications in a wide range of industries in the real world. There is considerable interest in the deployment of robots into hazardous situations, performing tasks that would be too dangerous for a human worker to attempt. However, AMRs have already made a considerable impact in the industrial world.
Autonomous robots are enabling the lights-out factory. A lights-out factory, also called a dark factory, is one where the need for human activity is so small that the facility can operate in the dark. Autonomous mobile robots are an integral part of the production line, employed to deliver raw materials around the factory. The independent nature of these robots allows them to respond to the latest requirements by calculating the optimum route through a complex and dynamic environment. A change in production schedule is automatically communicated to the fleet of delivery robots, ensuring that the right parts are in the right place at the right time.
The vision of a true “lights-off”, remotely operated factory is never quite achievable. While many aspects of production can be left to industrial automation, there are some aspects of the manufacturing process that require human intervention. Collaborative robots, often known as Cobots, have become a versatile and cost-effective technology that are designed to work alongside human operators. Their flexibility is powered by edgeAI and TinyML, allowing them to analyze processes in real-time and respond to the needs of the operator. They can increase productivity and respond more quickly to changing customer demands by relieving their human coworkers of the need to perform repetitive tasks.
Whether AMRs or Cobots, robots must keep operators safe, and this is the role of functional safety equipment. The goal of functional safety is to ensure that systems can operate efficiently without risking injury to operators. In the case of production equipment that is operated by computers, it is vital that the machinery is equipped with a range of devices that can respond immediately should an unsafe situation develop.
The first key component of safety systems will be sensors, which can take many forms. From simple door switches that detect if equipment is left in an unsafe condition to more sophisticated solutions including safety light curtains that serve as an alternative to physical barriers. These will detect if a foreign body – for example, the hand of an operator – enters a safety-critical space.
These sensors are only part of the solution, however. In an integrated smart factory, these sensors need to communicate quickly with other systems so that appropriate actions can take place without delay. This requires highly reliable connectors and cables that can provide the rapid communication necessary to ensure safety is maintained. They also require computing power that can respond with the minimum latency.
Planning for the Future
These have truly been challenging times for the electronics industry. The collapse of the air transport industry in the wake of the 2020 pandemic had measurable impacts on our global supply chain. At the same time, we saw a remarkable increase in demand as manufacturers took action to try and secure stock for the unknown future.
Within a year of the start of the pandemic, the supply chain was thrown into turmoil once again as a single event had global effects. It was a sobering realization that a single vessel, grounded in the Suez Canal, could cause huge delays for the shipping industry. Industry is still reeling from these events, and we continue to see shortages of a range of components. For many manufacturers, supply chain security has become as important as innovation.
The smart factory helps solve supply chain issues by making procurement an integral part of the design cycle. Artificial intelligence technology can be used to continually collect information about a customer’s chosen parts. It monitors global search activity to highlight parts that are – or will be – in high demand. It monitors availability and stock levels to warn designers if parts are hard to source. It takes input from component suppliers to alert the designer to possible End-of-Life notifications. It also searches through the global distribution channel to determine the most cost-effective source for each part.
Summary
One of the key benefits of smart technology is that it is easy to adopt in stages. The smart factory provides one of the clearest examples of this machine-to-machine communication at work, and the production line process that has dominated manufacturing for a hundred years lends itself well to this type of integration. Innovations in connectivity including plug-and-play functionality and Single Pair Ethernet (SPE) such as ADIN1110 MAC-PHY, ADIN1100 and ADIN2111 are making the integration of individual smart factory elements easier than ever.
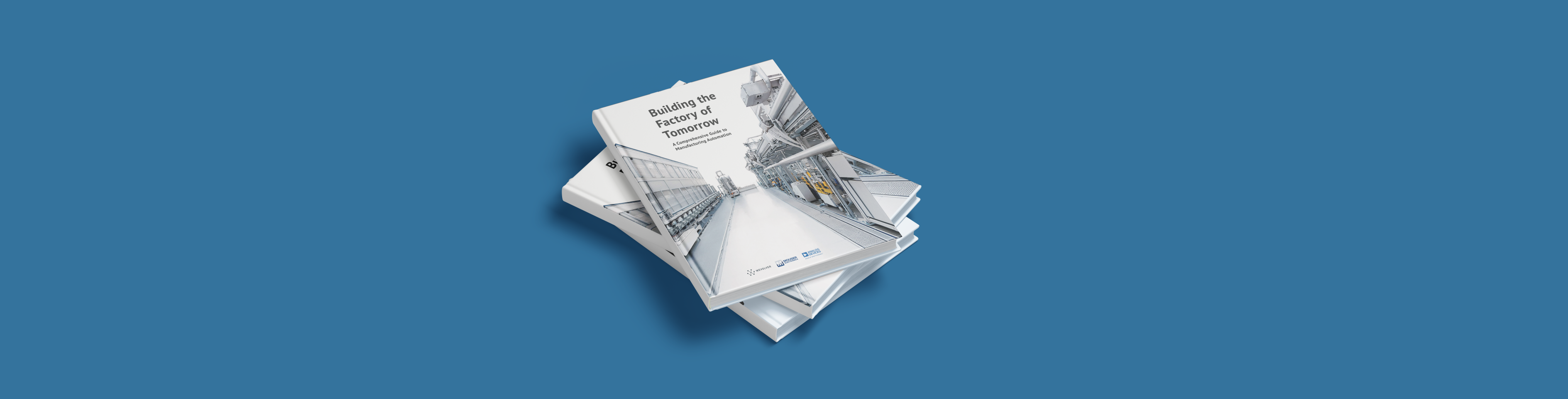