Our latest report, Building the Factory of Tomorrow, offers an in-depth analysis of the core forces shaping modern industrial production, from the accelerated pace of technological innovation to the integration of human-robot collaboration in next-generation factories.
Download this detailed report to explore:
- Cutting-edge advancements in AI, Quantum Computing, and Hyper Automation that are impacting manufacturing processes.
- The impact of globalized supply chains and virtual collaboration tools in enabling seamless cross-border operations.
- The shift toward sustainable production models, emphasizing circular value chains and carbon-neutral practices.
This report provides valuable technical insights for engineers, industry leaders, and decision-makers seeking to leverage the latest innovations and strategic trends to enhance operational efficiency and remain competitive in a rapidly changing landscape.
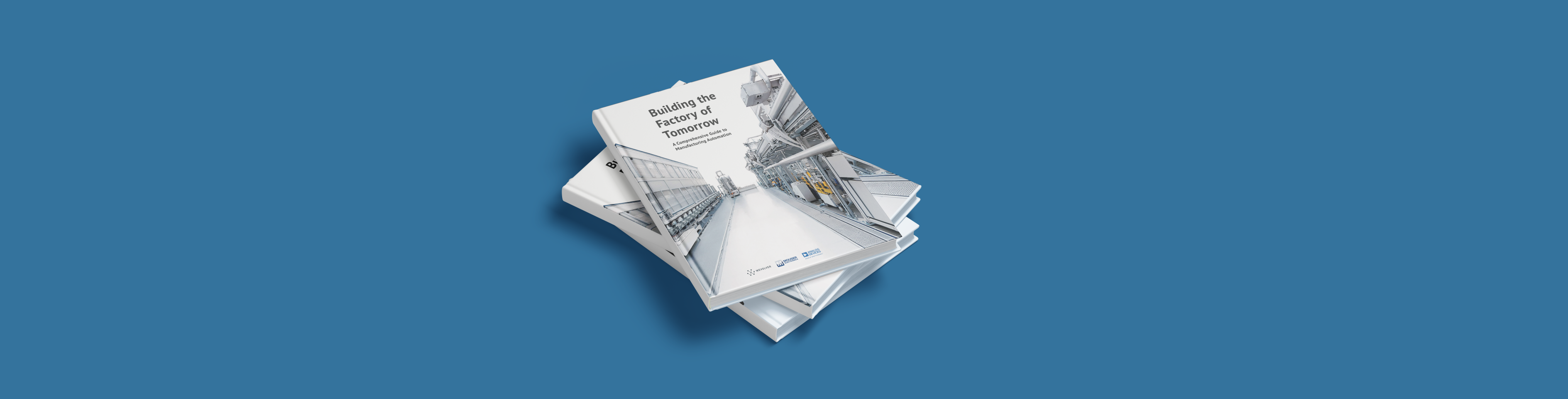
Modern manufacturing is undergoing a significant transformation as it embraces advanced technologies like cyber-physical systems, the Internet of Things (IoT), and artificial intelligence (AI). This integration, often referred to as Industry 4.0 and 5.0, is driving increased efficiency and customization but also introduces cybersecurity vulnerabilities and the need for stricter regulations.
Robust cybersecurity measures are crucial for protecting sensitive data and ensuring the integrity of automated systems against cyberattacks. These attacks can disrupt operations, cause financial losses, and damage a company's reputation. Additionally, adhering to relevant regulations like GDPR, CCPA, and the latest AI Ethics Standards is essential for legal compliance, building trust with customers and partners, and maintaining market access.
Manufacturers must effectively address these challenges to harness the full potential of Industry 4.0 and 5.0 while simultaneously ensuring their operations are secure, compliant, and adaptable. This chapter explores the critical role of cybersecurity and regulatory compliance in modern manufacturing.
Regulation and Standards in the Industry 4.0/5.0 Era
In the Industry 4.0 and forthcoming Industry 5.0 era, manufacturing has transcended traditional boundaries, embracing digital technologies to create interconnected, intelligent systems that promise unprecedented efficiency, productivity, and customization. However, this digital revolution also brings to the fore the critical necessity for stringent cybersecurity measures and robust regulatory compliance to safeguard these advanced manufacturing environments.
Overview of Applicable Regulations
Understanding and adhering to regulatory frameworks is essential for manufacturers, ensuring they meet compliance and uphold ethical standards in the deployment of the latest innovations. Some notable examples of such regulations include:
General Data Protection Regulation (GDPR)
The General Data Protection Regulation (GDPR), effective from May 25, 2018, in the European Union (EU), marks a milestone in data protection laws globally. It mandates strict data handling practices for manufacturers worldwide who process EU residents' data, emphasizing the importance of obtaining explicit consent, enabling individuals to manage their personal data, and implementing stringent cybersecurity protocols. The regulation aims to empower individuals with control over their personal data while streamlining the regulatory landscape for businesses operating across EU borders.
Manufacturers must integrate data protection measures from the beginning of the product and process design phase, ensuring privacy by default and minimizing data collection. The GDPR also sets severe penalties for violations, making data protection a critical concern at all levels of manufacturing operations, including supply chains and customer relations. The appointment of Data Protection Officers is essential for ensuring adherence to these practices, underlining the need for transparency and accountability in data processing activities.
California Consumer Privacy Act (CCPA)
Similar to the GDPR, the CCPA grants California residents enhanced rights over their personal data, including the rights to know, delete, and opt-out of the sale of their information. Manufacturers serving or employing California residents must comply, necessitating a reevaluation of data handling practices.
Key aspects include stringent requirements for notifying consumers about data collection processes and obtaining explicit consent for minors. The act also imposes penalties for non-compliance, underscoring the financial and reputational risks of data breaches. For manufacturers, this means embedding privacy considerations into operational and data management practices, ensuring transparency, and bolstering data security measures. The CCPA embodies a significant shift towards greater consumer control and privacy, setting a precedent for future state-level privacy laws in the United States.
AI Act
The AI Act by the EU marks a big regulatory move specifically targeting AI technologies. The manufacturing sector, which utilizes AI for automation, predictive maintenance, and supply chain optimization, must now align with the AI Act's mandates. This legislation emphasizes a risk-based classification for AI systems, aiming to calibrate regulations with the potential harm an AI system might cause, especially critical in manufacturing where risks can range widely.
Compliance with the AI Act for manufacturers will necessitate ensuring that AI systems are transparent and traceable and operate in ways that uphold EU standards for safety, privacy, and ethical practices. This approach highlights the necessity of human oversight in critical decision-making processes and advocates for the responsible management of data, urging the use of high-quality inputs to minimize biases and inaccuracies that could compromise product quality and safety.
Through its provisions for surveillance and penalties for non-compliance, the AI Act is set to enforce a safer, more regulated integration of AI in manufacturing, promoting an environment where innovation can flourish within defined parameters of safety and ethics.
Industrial Architectures and Standards
Industrial Architectures and Standards play a crucial role in shaping the future of manufacturing, offering frameworks and guidelines for integrating new technologies seamlessly and securely. Some examples of such architectures and standards are:
Reference Architectural Model Industrie 4.0 (RAMI 4.0)
Reference Architectural Model Industrie 4.0 (RAMI 4.0) is an innovative framework designed to navigate the complexities of the Fourth Industrial Revolution. By integrating the entire product lifecycle and factory hierarchy with layers of IT functionality, RAMI 4.0 offers a holistic approach to digital transformation in manufacturing. Unique to RAMI 4.0 is its three-dimensional mapping, facilitating a clear understanding of how digital and physical entities interact across different stages of production and levels of operation.
This model is pivotal in addressing the challenges of interoperability and security, ensuring that diverse systems can work together seamlessly and securely. Moreover, RAMI 4.0's emphasis on modular system design promotes flexibility, allowing for easy adaptation to technological advancements and changing business requirements. As a strategic tool, it not only streamlines the adoption of Industrie 4.0 technologies but also enhances collaboration among various stakeholders, propelling the manufacturing sector toward a more interconnected and efficient future.
Industrial Internet Reference Architecture (IIRA)
The Industrial Internet Reference Architecture (IIRA), developed by the Industrial Internet Consortium, offers a strategic blueprint for integrating digital technologies with industrial systems, focusing on the Industrial Internet of Things (IIoT). It addresses business goals, use cases, functional requirements, and implementation strategies for IIoT solutions, emphasizing interoperability, security, and scalability.
By promoting a cross-industry approach and advocating for the use of standards, the IIRA ensures seamless information flow across various platforms and devices, facilitating efficient and secure IIoT deployments. This framework supports organizations in achieving operational efficiency and competitive advantage through a structured yet adaptable methodology, bridging the gap between operational and informational technology domains in a secure and sustainable manner.
Manufacturing Automation Standards
Manufacturing automation standards are crucial for ensuring automated systems are reliable, safe, and efficient. Key standards like ANSI/ISA-95 (IEC 62264) and ISO/TC 184 serve distinct purposes:
ANSI/ISA-95 - IEC 62264: Enterprise-control system integration
ANSI/ISA-95, or IEC 62264, provides a technical framework for integrating enterprise and manufacturing operations systems, focusing on the seamless exchange of information between Enterprise Resource Planning (ERP) and Manufacturing Execution Systems (MES) layers. Central to its framework is the facilitation of communication between Information Technology (IT) and Operational Technology (OT) systems, a key aspect in maintaining cybersecurity and enhancing operational efficiency.
By defining a detailed data model and specifying interface requirements, including function blocks, data types, and communication protocols, the standard ensures interoperable and scalable integration. It provides activity models for various manufacturing operations and object models for consistent data representation, supporting standardized industry operations.
ANSI/ISA-95 addresses cybersecurity concerns by safeguarding data integrity and confidentiality during exchanges across different organizational layers. This comprehensive approach bolsters operational performance and plays a pivotal role in the digital transformation of manufacturing environments, underlining its significance in contemporary industrial IT strategies.
ISO/TC 184 Automation systems and integration
ISO/TC 184 Automation Systems and Integration is a technical committee of the International Organization for Standardization (ISO) dedicated to creating standards for the seamless interoperability of automation systems across industries. ISO/TC 184 focuses on the broader scope of automation systems and their integration across various industries. Unlike ANSI/ISA-95, which zeroes in on integrating enterprise and control systems, ISO/TC 184 encompasses a wide array of automation aspects.
It aims to standardize the interoperability of automation systems, enhancing productivity and supporting digital transformations across the board. While ANSI/ISA-95 is concentrated on manufacturing processes, ISO/TC 184's standards, such as ISO 10303 for product data, ISO 13374 for condition monitoring, and ISO 15745 for automation integration, apply to a broader spectrum of industrial automation. This makes ISO/TC 184 pivotal in promoting global compatibility and operational excellence in a more extensive range of automated systems.
Cybersecurity Standards
Cybersecurity standards provide essential guidelines for safeguarding manufacturing systems and data against cyber threats. Examples of such standards are:
ISO/IEC 27000 Family: Information security management
In the manufacturing sector, the ISO 27000 series, specifically ISO/IEC 27001, plays a crucial role in safeguarding sensitive data, ranging from proprietary designs to customer information. This set of standards provides manufacturers with a systematic framework for managing information security risks, enhancing cybersecurity measures, and ensuring compliance with regulatory requirements.
Implementing an Information Security Management System (ISMS) as outlined in ISO/IEC 27001 enables manufacturing organizations to protect against data breaches, intellectual property theft, and cyber-attacks, thereby securing their supply chains and production processes.
NIST 800-37: Risk Management Framework for Information Systems and Organizations
NIST Special Publication 800-37 introduces the Risk Management Framework (RMF), offering a systematic approach to managing cybersecurity risks that is applicable across various sectors, including manufacturing. This framework guides organizations through identifying, assessing, and mitigating risks to their digital assets and operations. For manufacturers, implementing the RMF can significantly enhance the protection of sensitive data, intellectual property, and production processes against cyber threats. It promotes a proactive stance on cybersecurity, focusing on continuous monitoring and improvement. By integrating NIST 800-37's principles, manufacturing firms can safeguard their increasingly digitized and interconnected operations, maintaining resilience in a rapidly evolving cyber landscape.
IEC 62443: "Security for industrial automation and control systems"
Contrary to ISO 27000 and NIST 800-37 which are general security standards that are applicable to multiple sectors, the IEC 62443 series of standards is focused on securing industrial automation and control systems (IACS) throughout their entire lifecycle. In this direction, the standard prescribes and supports a quite wide range of security functions including risk assessment, security management, and technical measures at both the component and the system levels. IEC 62443 comprises nine standards, along with technical reports and technical specifications.
The IEC 62443 standards can play a key role for the Factories of the Future towards securing Industry 4.0 / Industry 5.0 use cases through enhancing the security posture of industrial systems, increasing resilience against cyber threats, protecting critical infrastructures in the scope of industrial sites, minimizing downtimes, prolonging equipment lifespan and fostering interoperability and flexibility. Furthermore, compliance with IEC 62443 mandates can greatly boost compliance with legal and regulatory requirements such as with data protection, industrial safety, and AI-related regulations.
AI Ethics Standards
IEEE 7000: Addressing Ethical Concerns during System Design
This standard addresses ethical considerations in the design and deployment of AI systems, focusing on transparency, accountability, and privacy. For the manufacturing sector, adhering to IEEE 7000 standards ensures that AI applications in automation are developed and used ethically, respecting the principles of human rights and societal values.
While the AI Act focuses on regulatory compliance and legal frameworks for AI applications, ensuring that AI systems are safe, transparent, and nondiscriminatory across the EU, the IEEE 7000 emphasizes ethical guidelines for the development and deployment of AI and autonomous systems, promoting principles like transparency, accountability, and privacy across all sectors, including manufacturing.
Ethics Guidelines for Trustworthy AI by the European Commission's High-Level Expert Group on AI
These guidelines are crucial due to their backing by the European Commission and their comprehensive framework for achieving trustworthy AI. They emphasize critical principles such as human agency and oversight, technical robustness, privacy, transparency, diversity, and environmental well-being. The guidelines have a significant impact on policy and regulatory approaches to AI in Europe and beyond, setting a high standard for ethical AI development and deployment.
The regulatory and standards landscape in the Industry 4.0 and 5.0 era is complex but essential for manufacturers to understand and comply with. These regulations and standards ensure the security and privacy of data and systems and foster trust among consumers, partners, and regulatory bodies. By adhering to these guidelines, manufacturers can leverage the full potential of digital transformation while mitigating risks and ensuring their operations are efficient and secure.
Ensuring Compliance with Regulations and Standards
Effectively managing compliance with the regulations and standards governing the manufacturing sector is a complex but crucial task. Manufacturers must adhere to stringent data protection laws, cybersecurity mandates, and ethical guidelines, all while striving to maintain operational efficiency.
Integrating Compliance into Business Processes
Successful manufacturers integrate compliance requirements directly into their business processes. This involves embedding data protection and privacy measures, cybersecurity protocols, and AI ethics considerations into the design phase of product development and throughout the manufacturing process. By adopting a "privacy by design" and "security by design" approach, manufacturers can ensure compliance is an inherent aspect of their operations, reducing the risk of non-compliance and the need for costly retroactive measures.
Leveraging Technology for Compliance
Advanced technologies such as AI and blockchain can be harnessed to streamline compliance efforts. AI can analyze vast amounts of data to ensure adherence to regulations like GDPR and CCPA, identifying potential compliance issues before they become problematic. On the other hand, Blockchain offers unparalleled data integrity and traceability, which are crucial for meeting stringent regulatory requirements in manufacturing processes.
Continuous Compliance Monitoring
Compliance is not a one-time effort but a continuous process. Implementing continuous monitoring systems allows manufacturers to stay abreast of their compliance status with regulations and standards. These systems can detect deviations from compliance in real-time, enabling immediate corrective actions to be taken, thereby minimizing the risk of regulatory penalties and reputational damage.
Building Trust with Certifications
Certifications based on recognized standards, such as ISO 27001 for information security management, serve as a testament to a manufacturer's commitment to compliance and cybersecurity. Achieving certification can significantly enhance trust among customers, partners, and regulatory bodies, providing a competitive edge in the market.
In many cases, certifications are not just beneficial but necessary for market access. Certain regions and sectors may require compliance with specific standards as a prerequisite for doing business. Manufacturers with relevant certifications can navigate these requirements more smoothly, expanding their market presence and ensuring compliance across different jurisdictions.
The Importance of Cybersecurity
As manufacturing processes become increasingly digitized and interconnected, the importance of cybersecurity in protecting these environments cannot be overstated. Cybersecurity measures safeguard sensitive data, intellectual property, and the physical integrity of manufacturing systems against cyber threats. Implementing robust cybersecurity protocols is essential for preventing data breaches, industrial espionage, and sabotage, which could have devastating effects on operations and brand reputation.
Best Practices and Technologies for Secure Manufacturing Operations
In digitally interconnected manufacturing, securing factory operations against cyber threats is crucial. As manufacturers embrace automation and integrate cyber-physical systems, IoT devices, and AI into their processes, the complexity and scope of cybersecurity challenges grow. Addressing these challenges requires a combination of best practices and advanced technologies tailored to the unique needs of the manufacturing sector.
Data Provenance and Traceability
Data provenance, the ability to trace and verify the source and history of data, is critical in manufacturing to ensure the integrity and security of the information used in production processes. Implementing systems that provide complete traceability of data helps identify anomalies, prevent data tampering, and ensure compliance with regulations that demand transparency.
Blockchain technology stands out for its ability to offer immutable data records, ensuring data integrity across the supply chain. By leveraging blockchain, manufacturers can create a tamper-proof ledger of transactions, movements, and changes in data, providing a robust framework for data provenance and traceability.
Risk Assessment
A comprehensive risk assessment is the foundation of any effective cybersecurity strategy. Manufacturers should conduct regular assessments to identify potential vulnerabilities within their systems, including hardware, software, and network infrastructures. By understanding the likelihood and impact of different types of cyber threats, manufacturers can prioritize their cybersecurity efforts effectively.
Utilizing frameworks such as NIST’s Cybersecurity Framework helps in organizing and implementing risk assessment processes. Automated risk assessment tools can also play a crucial role inenabling continuous monitoring and analysis of threats in real-time, allowing manufacturers to adjust their security measures dynamically.
Cybersecurity Policies
Developing comprehensive cybersecurity policies is essential for setting the standards and expectations for security within an organization. These policies should cover all aspects of cybersecurity, from employee behavior and access controls to the management of IoT devices and the protection of sensitive data.
Training and Awareness
Cybersecurity is not just a technical challenge but also a human one. Regular training and awareness programs are crucial to ensure that all employees understand the cybersecurity policies and their role in maintaining security. Simulated cyber-attack exercises can also help in testing the effectiveness of policies and the readiness of the team to respond to incidents.
Operational Technology Security
Securing OT, the hardware and software that monitors and controls physical devices and processes, requires specialized security measures. OT systems often have different characteristics and requirements than traditional IT systems, including the need for real-time performance and high availability.
Network segmentation is a critical strategy, isolating sensitive production systems from other parts of the network to limit the spread of potential attacks. Secure remote access solutions are also vital, ensuring remote maintenance and monitoring activities do not open up vulnerabilities in OT systems.

Adopting Cutting-Edge Technologies for Cybersecurity
AI and machine learning can significantly enhance a manufacturer's cybersecurity capabilities. These technologies can analyze patterns in data to identify potential threats more quickly than traditional methods, predict attacks before they happen, and automate responses to detected threats, improving the speed and efficiency of cybersecurity operations.
Fortifying Manufacturing with Real-Time Intrusion Detection and Prevention
Intrusion Detection Systems (IDS) and Intrusion Prevention Systems (IPS) are critical components of a comprehensive cybersecurity strategy. These systems monitor network and system activities for malicious activities or policy violations, providing real-time protection against a wide range of cyber threats.
Endpoint Detection and Response (EDR) solutions offer continuous monitoring and response capabilities for endpoints, such as mobile devices, computers, and IoT devices, that are often the targets of cyberattacks. EDR solutions can detect, investigate, and respond to cybersecurity threats, providing an additional layer of security.
Implementing these best practices and technologies requires a strategic approach tailored to the specific needs and challenges of the manufacturing sector. By prioritizing data provenance and traceability, conducting thorough risk assessments, establishing comprehensive cybersecurity policies, and employing advanced technologies, manufacturers can create a resilient cybersecurity posture.
Regular Compliance Audits and Assessments
Conducting regular audits and assessments of compliance measures is essential to ensure ongoing adherence to regulations and standards. These audits help identify gaps, weaknesses, or areas for improvement, allowing manufacturers to proactively address compliance issues before they escalate.
Incident Response and Contingency Planning
Despite preventive measures, incidents such as data breaches or compliance violations may occur. Manufacturers must have robust incident response plans in place to address and mitigate the impact of such incidents swiftly. This includes procedures for reporting, investigating, and remedying incidents, as well as communication protocols for stakeholders.
Future Trends and Challenges
As the manufacturing sector progresses deeper into Industry 4.0 and moves towards Industry 5.0, it faces certain rapidly changing trends and challenges, especially in cybersecurity and regulatory compliance. These developments are driven by technological innovations, changing regulatory landscapes, and the sophisticated nature of cyber threats.
Increased Integration of IoT and Edge Computing
The expansion of the IoT and edge computing in manufacturing operations will continue to grow, offering enhanced data processing capabilities at the network's edge. This trend promises real-time insights and decision-making support but also introduces new vulnerabilities and attack surfaces for cyber threats. Securing these devices using encryption processors such as the DS28S60 DeepCover Cryptographic Coprocessor and MAXQ1065 Ultra Low-Power Cryptographic Controller to ensure their compliance with regulatory standards will be a primary focus for manufacturers.
Advancements in AI and Machine Learning
Advancements in AI, such as the rising prominence of Large Language Models (LLMs), and Edge AI are set to revolutionize manufacturing by significantly enhancing both operational efficiency and cybersecurity defences.
Edge AI facilitates predictive maintenance, streamlines production processes, and enables personalized manufacturing approaches, transforming industrial operations in ways that seemed impossible until now. By leveraging these models, manufacturers can anticipate maintenance needs, optimize workflows, and tailor products to individual specifications, which boosts productivity and security.
When it comes to cybersecurity, LLMs are invaluable for analyzing vast data to swiftly detect and respond to threats, minimizing potential damage. They can be used to automate incident responses and generate tailored educational content for security training. Additionally, LLMs assist in navigating complex regulatory conditions, ensuring compliance with industry standards, and facilitating clear communication during cyber incidents. Their ability to rapidly process and interpret complex information is crucial for maintaining robust cybersecurity defences and ensuring operational continuity.
However, the integration of LLMs in manufacturing also raises ethical concerns and regulatory scrutiny. Issues such as data privacy, algorithmic transparency, and decision-making accountability are pivotal, highlighting the need for careful consideration and management of these advanced AI technologies in sensitive industrial environments.
Resilient Manufacturing with Digital Supply Chains
The relationship between resilient manufacturing, supply chains, and cybersecurity has become a crucial area of focus following the disruptions caused by the COVID-19 pandemic and recent geopolitical conflicts.
The shift towards digitalization in manufacturing has significantly increased dependency on technologies such as IoT, AI, and cloud computing. This digital transformation is essential for resilient supply chains but also exposes businesses to heightened cybersecurity risks. As manufacturers adopt these technologies, the entire supply chain becomes a potential target for cybercriminals. Attacks on any part of the chain can have widespread, disruptive effects.
To address these challenges, manufacturers must implement adaptive cybersecurity strategies that include continuous monitoring and real-time threat detection. This approach helps in dynamically responding to evolving threats, ensuring both the security of operations and the integrity of data across the supply chain.
Moreover, enhancing cybersecurity in this interconnected environment requires collaboration. Manufacturers should engage in sharing information about threats and vulnerabilities with industry peers and governmental bodies. This collective effort in cybersecurity can significantly strengthen the defense mechanisms across all nodes of the supply chain, leading to a more resilient manufacturing ecosystem in the face of global uncertainties.
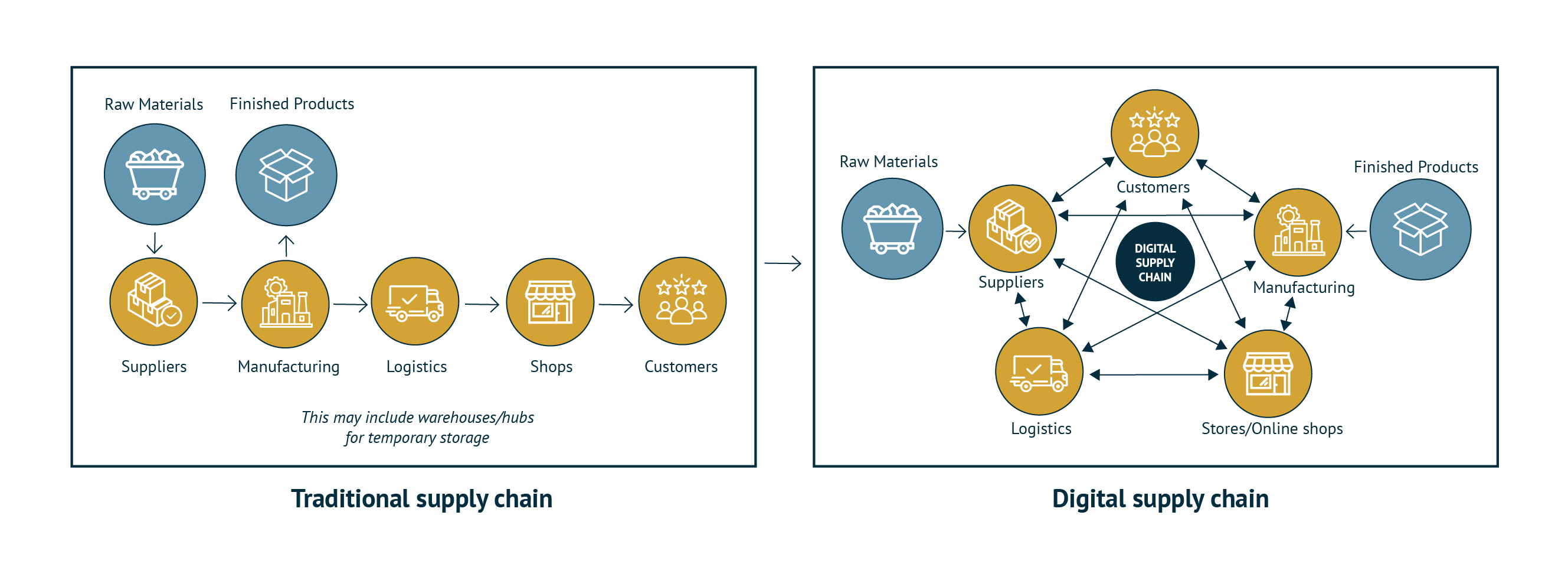
Adapting to Regulatory Changes
The regulatory environment for cybersecurity and privacy is expected to become more complex, with new laws and standards being introduced. Manufacturers must remain agile, adapting their compliance strategies to meet these changing requirements without compromising operational efficiency.
Implementing Modular Manufacturing Systems
Modular manufacturing, characterized by its plug-and-play components such as networks, sensors, and data analytics algorithms, significantly enhances flexibility in production systems. This approach allows manufacturers to swiftly adapt to changing market demands and technological advancements. By integrating modular components, companies can efficiently update or replace specific parts of the production line without overhauling the entire system, thus minimizing downtime and boosting productivity.
However, the increased connectivity and interoperability pose heightened cybersecurity risks. Each modular component could potentially serve as an entry point for cyber threats. Therefore, robust cybersecurity measures are essential to protect against data breaches and ensure the integrity of manufacturing operations.
Mitigating Advanced Cyber Threats
Cyber threats are becoming more sophisticated, with attackers leveraging AI and machine learning to conduct their operations. Manufacturers must continuously evolve their cybersecurity measures to protect against these advanced threats, including ransomware, phishing attacks, and industrial espionage.
Ensuring Compliance Across Borders
As manufacturers operate globally, navigating the regulatory conditions across different jurisdictions becomes increasingly complex. Ensuring compliance with varying international standards and regulations poses a significant challenge, requiring a comprehensive understanding and strategic approach to regulatory adherence.
Securing the Future of Manufacturing
To successfully address these trends and challenges, manufacturers must invest in continuous learning and innovation, adopt flexible and resilient cybersecurity strategies, and engage in proactive regulatory compliance management. Doing so can safeguard their operations against emerging threats and ensure their continued growth and competitiveness in the digital manufacturing era.
The increasing digitalization of manufacturing processes in Industry 4.0 and 5.0 presents a new challenge: ensuring robust cybersecurity while complying with evolving regulations. As technological advancements continue to redefine manufacturing, embracing best practices and cutting-edge technologies for cybersecurity while staying agile in response to evolving regulatory standards is essential.
By prioritizing data integrity, operational security, and compliance, manufacturers can fortify their operations against cyber threats and guarantee smooth market access. This proactive stance goes beyond mere asset protection; it's a strategic investment in the future resilience and prosperity of manufacturing in the digital era.
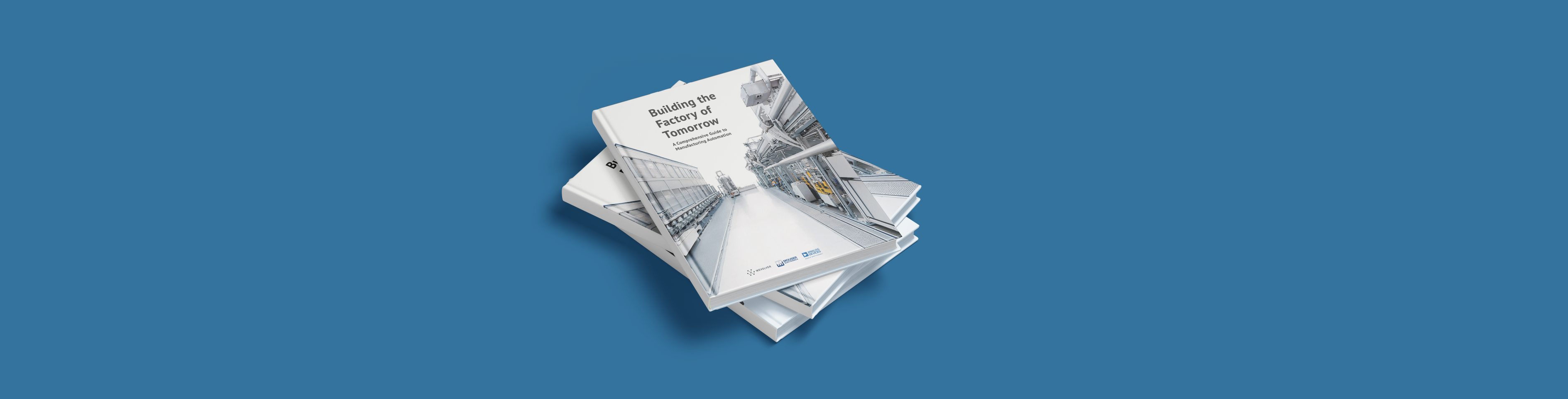