Our latest report, Building the Factory of Tomorrow, offers an in-depth analysis of the core forces shaping modern industrial production, from the accelerated pace of technological innovation to the integration of human-robot collaboration in next-generation factories.
Download this detailed report to explore:
- Cutting-edge advancements in AI, Quantum Computing, and Hyper Automation that are impacting manufacturing processes.
- The impact of globalized supply chains and virtual collaboration tools in enabling seamless cross-border operations.
- The shift toward sustainable production models, emphasizing circular value chains and carbon-neutral practices.
This report provides valuable technical insights for engineers, industry leaders, and decision-makers seeking to leverage the latest innovations and strategic trends to enhance operational efficiency and remain competitive in a rapidly changing landscape.
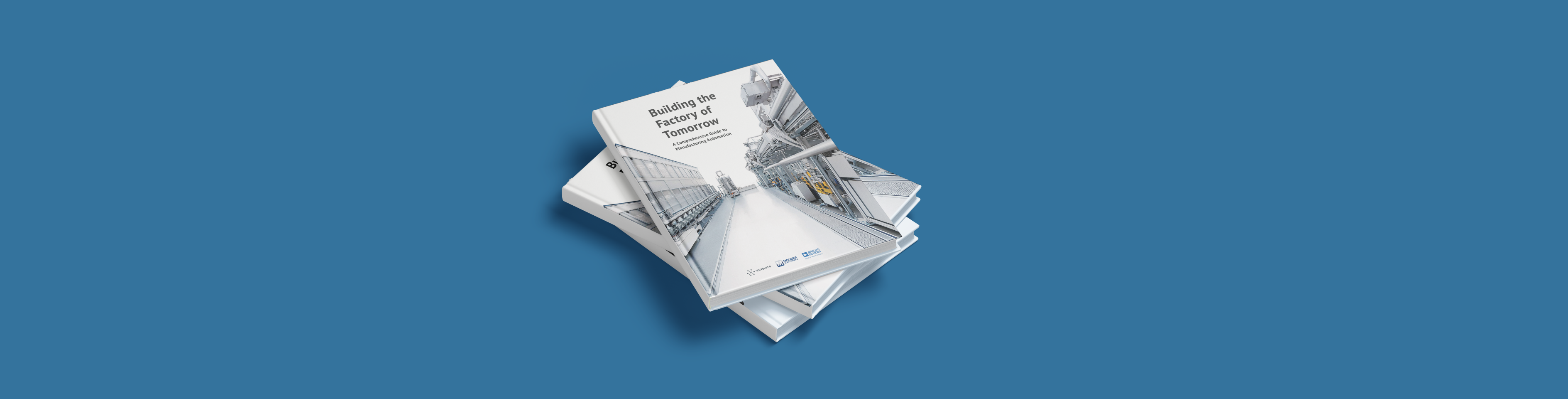
In the next decade, manufacturers and providers of industrial automation solutions will increasingly invest in Industry 4.0 and Industry 5.0. However, before embarking on such projects and initiatives manufacturers must be convinced that the new systems will improve production time, quality, and cost. In this direction, it will be very important for stakeholders to assess the potential return on investment (ROI) of Industry 4.0/5.0 projects and to ensure their viability. Capital budgeting methods provide an initial base for such ROI calculations and related feasibility studies. The following sub-paragraphs provide some of the most popular capital budgeting techniques.
Return on Investment (ROI)
ROI is a widely used capital budgeting method that calculates the percentage return earned on the invested capital. The formula for ROI is:
ROI = (Net Profit / Initial Investment) * 100
where Net Profit corresponds to the difference between the benefits and costs of the investment. To account for costs, both explicit and implicit costs should be considered. Explicit costs include hardware, software, and IT infrastructure investments, while implicit costs may comprise labour, training, and maintenance. In general, the key to ROI calculations is the consideration of the Total Cost of Ownership (TCO) of a manufacturing solution including upfront capital expenses and operating expenses for the useful life of the Industry 4.0/5.0 project.
Internal Rate of Return (IRR)
IRR determines the discount rate at which the net present value (NPV) of an Industry 4.0 project becomes zero. In other words, it is the rate at which the project breaks even. To account for costs, the initial investment and cash flows are discounted using an appropriate discount rate, which typically considers the inflation rate and the time value of money. The IRR is the rate that makes the NPV equal to zero.
Payback Method
The payback method measures the time required to recover the initial investment. It considers the cash inflows of a project until the cumulative inflows equal or surpass the initial investment. Although simple, the payback method does not account for the time value of money, which is its main limitation.
Benefit Analysis
Cost/benefit analysis compares the costs and benefits of a project to determine its feasibility. Costs need to be carefully estimated and include direct costs (e.g., equipment, implementation, and maintenance) as well as indirect costs (e.g., labour, training, legal costs, and potential disruptions).
Profitability Index
The profitability index calculates the present value of expected cash inflows relative to the initial investment. It is very useful for comparing different projects and Industry 4.0 investment opportunities. As such it enables decision-makers (e.g., the manufacturer’s business management) to select the projects with the highest profitability. Costs associated with the project should be accurately estimated to ensure the reliability of the profitability index calculation and the credibility of the related project selection decisions.
Challenges and Limitations of Capital Budget Methodologies for Industry 4.0 Projects
The above-listed ROI estimation methods are proven and widely used in the industry. However, measuring the potential monetary benefits of Industry 4.0/5.0 projects is very challenging for a variety of reasons. First and foremost, it is very difficult to accurately estimate the monetary benefits of a high-tech manufacturing project. Uncertainty and unforeseen factors, such as market dynamics, technological advancements, and evolving customer demands, may impact the project's outcomes. Moreover, calculations remain sensitive to potential supply chain disruptions and other unexpected events. As a result, projecting future cash flows and benefits with precision can be demanding. Any inaccurate estimations can lead to misleading ROI calculations and affect the decision-making process.
Another challenge relates to the quantification of intangible benefits. Industry 4.0 projects often introduce intangible benefits that are difficult to quantify in monetary terms. For example, improved product quality, enhanced customer satisfaction, and streamlined processes may lead to intangible benefits such as better strategic positioning and improved brand image. While the latter benefits contribute to overall business performance, it is very difficult to quantify them in a credible way.
Also, capital budgeting methodologies rely on several assumptions to simplify calculations and reduce complexity. These assumptions may not always accurately capture the real-world complexities and dynamics of projects, leading to a potential bias in the results. Furthermore, these methodologies often focus on internal project factors while neglecting external factors that may influence the project's success. For example, market shifts, regulatory changes, and competitor actions can significantly impact the financial performance and longevity of an Industry 4.0/5.0 project. However, these external factors are sometimes very hard to predict and are almost impossible to be properly quantified. Note also that some capital budgeting methods (e.g., the payback method), do not account for the time value of money. Failing to consider the diminishing value of money over time can lead to suboptimal decision-making, especially when projects have different durations or vary significantly in their cash flow patterns.
There are also manufacturing scenarios where capital budgeting results are sensitive to the accuracy of the input data and assumptions made during the estimation process. In many cases, small changes in estimates or assumptions can cause significant variations in calculated ROI or profitability indices. Sensitivity analyses should be therefore conducted to assess the impacts of such changes.
From ROI to Social-ROI for Sustainability Assessment Methods
Industry 5.0 scenarios and applications put emphasis on sustainability and environmental performance. Likewise, the evaluation of Industry 5.0 projects must consider and assess both social and economic parameters. Specifically, rising environmental concerns, resource scarcity, and social expectations, lead manufacturers to prioritize sustainable practices in their operations and to undertake relevant investments. For instance, modern manufacturers are increasingly investing in “green” products that leverage eco-friendly materials to reduce their environmental impact. Such materials are typically sourced sustainably and are recyclable or biodegradable, minimizing waste and pollution. Some of the most prominent examples of such materials include bioplastics, natural fibers, and recycled materials. Nevertheless, the selection and use of such materials is likely to incur additional costs that may compromise the ROI of the relevant production processes.
Manufacturers are also investing in “Sustainability by Design'' i.e., the integration of sustainable principles at every stage of the product life cycle. This involves considering environmental impact, resource efficiency, and social factors end-to-end i.e., during product development, manufacturing, packaging, transportation, and end-of-life disposal. Similar to the case of eco-friendly materials, the adoption of sustainable practices requires additional investments and costs.
Industrial enterprises can however account for direct gains based on their sustainability practices and investments. For example, minimizing waste is essential to achieving sustainability goals. Techniques like lean manufacturing, process optimization, and efficient resource utilization can help reduce waste generation and increase overall efficiency, which can translate to monetary benefits. Moreover, they can also benefit from circular economy processes such as reusing and remanufacturing waste materials. The latter involves processing and refurbishing discarded products or components to create new usable products. This reduces the demand for new resources and minimizes waste disposal, which leads to tangible economic benefits.
Overall, Industry 5.0 projects must be evaluated not only based on monetary terms but also based on the social value that they generate. To this end, the scope of ROI calculations must be extended with social elements towards Social ROI (S-ROI). S-ROI expands a project’s evaluation scope beyond traditional financial measures to incorporate social and environmental impacts. It assesses the positive social, environmental, and economic outcomes resulting from a project. Evaluating and factoring the sustainability outcomes in the ROI analysis helps ensure that the long-term benefits and impacts on society and the environment are considered alongside financial returns.
S-ROI allows decision-makers to prioritize projects that align with sustainability goals, maximize positive social and environmental outcomes, and mitigate negative impacts. It fosters responsible and sustainable decision-making while creating value for multiple stakeholders, including employees, customers, communities, regulators, and the natural environment. The S-ROI calculation process includes the following steps:
Metrics Identification: This step selects relevant metrics to measure the project's impact. These include indicators like greenhouse gas emissions reduction, energy savings, waste reduction, community engagement, job creation, and social equity, as well as other relevant social and environmental factors.
Baselines Establishment: In this step baseline data for the chosen metrics are determined. This establishes the starting point against which manufacturers will measure the project's impact. Moreover, relevant data for comparison before (as-is) and after (to-be) the project implementation are collected.
Impact Quantification: This step measures the actual impact of the project on the chosen metrics. It assesses the changes or improvements observed as a result of implementing sustainable practices, technology upgrades, or process optimizations. This involves data collection, surveys, interviews, and analysis.
Values Assignment: Assign a value or monetary equivalent to the measured impacts. This step involves determining the monetary or social value of the positive changes resulting from the project. This can be challenging, and consultation with experts or stakeholders might be necessary.
S-ROI Calculation: The ROI can be adapted to account for social and environmental impacts. Any calculations must consider the total benefits (measured impacts) and costs associated with the project, including financial, social, and environmental costs. The calculated S-ROI will reflect the project's overall effectiveness in delivering positive social and environmental outcomes compared to the investment made.
Communicate and Report: The S-ROI analysis and findings must be clearly and transparently communicated to relevant manufacturing stakeholders, decision-makers, and the public. Emphasis should be placed on the positive social and environmental benefits generated by the project.
ESG Factors for the Manufacturing Industry
Beyond S-ROI analysis there are also other sustainability metrics that measure and evaluate environmental, social, and governance performance indicators of an organization. These metrics provide tangible data to assess the impact of sustainability practices and determine areas for improvement. Nowadays, there is a lot of emphasis on ESG (Environmental Social, and Governance) indexes, which aggregate such metrics to rank companies' sustainability performance for investors and other relevant stakeholders.
In general, calculating ESG (Environmental, Social, and Governance) Indexes involves aggregating data from various sources and applying specific methodologies to assess a company's sustainability performance. Here is an overview of common methods used to calculate ESG indexes and produce ESG factors and rankings:
Data Collection: This involves gathering data on environmental, social, and governance factors from relevant sources. Such sources include company reports, public disclosures, third-party databases, and sustainability rating agencies. Relevant datasets span a wide range of metrics, similar to the metrics used for S-ROI calculation.
Standardization: This step ensures that the collected data is standardized and comparable across companies and sectors. It involves normalizing the data to account for differences in company size, industry, geographical location, or other relevant factors.
Weighting: This step assigns weights to different ESG factors based on their significance and relevance to the overall sustainability framework. It also involves determining the relative importance of each factor and its contribution to the overall ESG performance.
Scoring: This involves assigning scores to companies based on their performance in each ESG factor. Scores can be derived using various methods, such as absolute scoring (e.g., fixed scale), relative scoring (i.e., performance compared to peers), or percentile-based scoring (i.e., based on performance ranking).
Aggregation: This step combines the scores of individual ESG factors to calculate an overall ESG score for each company. Aggregation methods can involve weighted averages, linear or non-linear models, as well as customized algorithms tailored to the specific ESG Index.
Ranking: This step ranks companies based on their overall ESG scores. It involves ordering companies from highest to lowest based on their ESG performance. Rankings allow for easy comparison and identification of top performers.
Index Construction: Formulate the ESG Index by selecting a subset of companies based on predefined criteria. The index focuses on specific sectors, regions, market capitalization, or other relevant factors. Companies are included in the index based on their ESG scores and rankings.
Regular Updates: This step is about maintaining the ESG Index by regularly updating the data, factors, and rankings. ESG Indexes are generally reviewed and recalibrated periodically to reflect the latest sustainability performance of companies.
Different providers and organizations may use variations of the above-listed methods to calculate ESG Indexes. The methodologies can differ in terms of factors considered, weighting schemes, scoring approaches, and criteria for index inclusion. Transparency and clear documentation of the methodology used are crucial to ensure the reliability and consistency of ESG Indexes. ESG research firms, rating agencies, and specialized ESG index providers are often responsible for creating and maintaining ESG Indexes. Investors, financial institutions, and companies can access these indexes to evaluate sustainability performance and make informed investment decisions aligned with their ESG goals.
The manufacturing industry has specific peculiarities when it comes to ESG factors and calculations. As a prominent example, manufacturing companies often have significant environmental impacts due to their resource consumption, waste generation, and emissions. Hence, ESG factors for the manufacturing industry typically include factors associated with energy efficiency, waste management, water usage, air quality, and climate change mitigation efforts. Moreover, manufacturing companies have complex and globally distributed supply chains. Hence, ESG factors within the supply chain must be assessed, including evaluating suppliers' sustainability practices, ethical sourcing, labour conditions, and potential environmental and social risks.
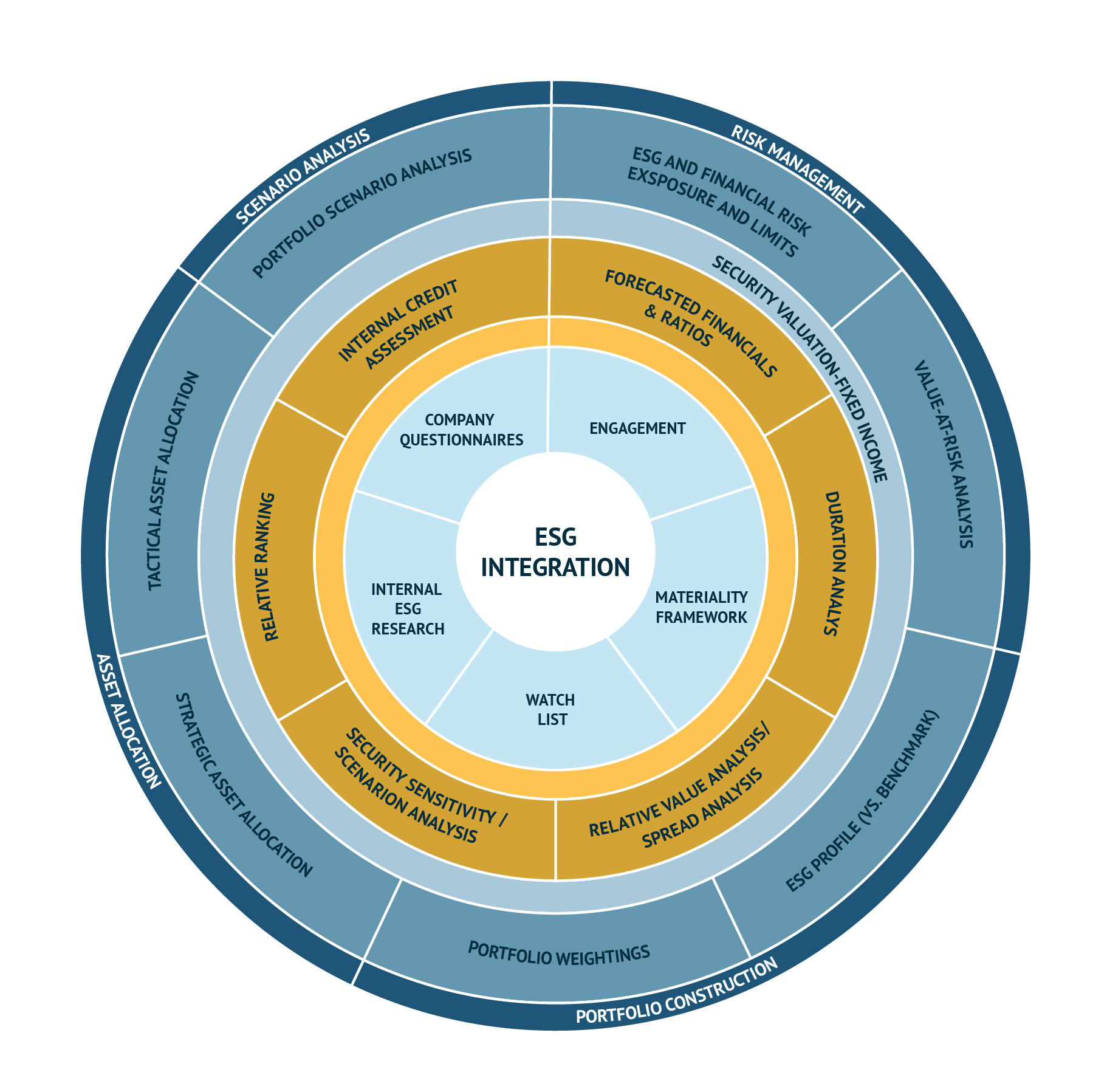
Also, manufacturing environments can pose various health and safety risks to workers. Occupational health and safety practices and indicators are therefore important ESG considerations in the manufacturing industry. This includes workplace safety measures, training programs, injury rates, and initiatives to improve employee well-being. Furthermore, manufacturing processes often involve a diverse workforce and global operations. Thus, evaluating human rights practices, labour rights, fair wages, and worker empowerment is integral to understanding the social aspect of ESG performance.
Finally, ESG calculations in the manufacturing industry must consider compliance with environmental regulations, health and safety standards, and labour law. Hence, ESG assessments must take into account a company's track record in adhering to relevant regulations and engaging in responsible business practices.
Overall, Industry 4.0 and Industry 5.0 in the factories of the future shall be evaluated in terms of their technical, financial, and social performance. This will require going beyond conventional ROI metrics to social return on investment and ESG factors.
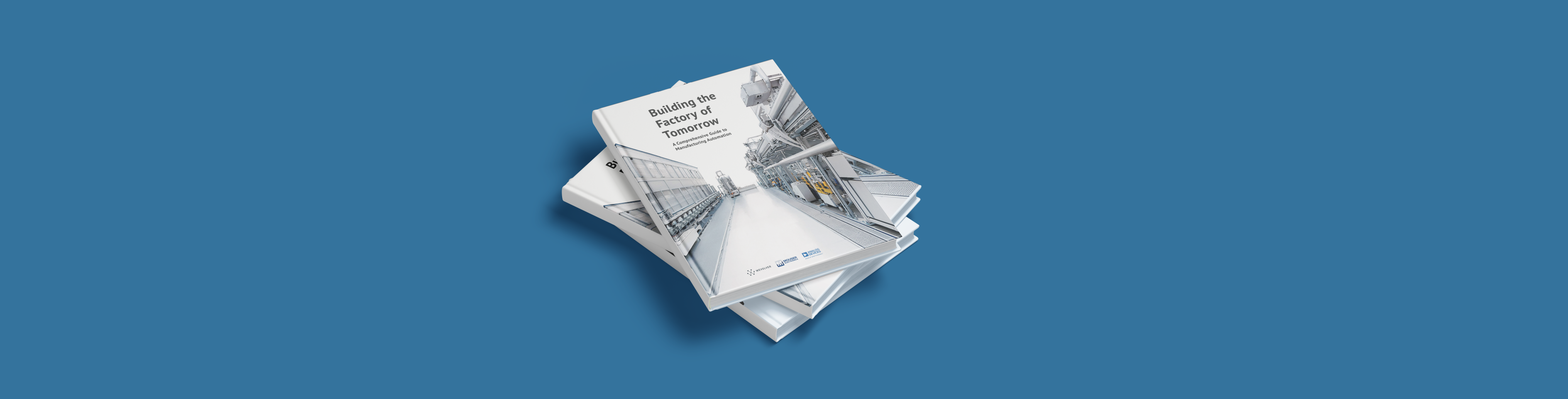