Our latest report, Building the Factory of Tomorrow, offers an in-depth analysis of the core forces shaping modern industrial production, from the accelerated pace of technological innovation to the integration of human-robot collaboration in next-generation factories.
Download this detailed report to explore:
- Cutting-edge advancements in AI, Quantum Computing, and Hyper Automation that are impacting manufacturing processes.
- The impact of globalized supply chains and virtual collaboration tools in enabling seamless cross-border operations.
- The shift toward sustainable production models, emphasizing circular value chains and carbon-neutral practices.
This report provides valuable technical insights for engineers, industry leaders, and decision-makers seeking to leverage the latest innovations and strategic trends to enhance operational efficiency and remain competitive in a rapidly changing landscape.
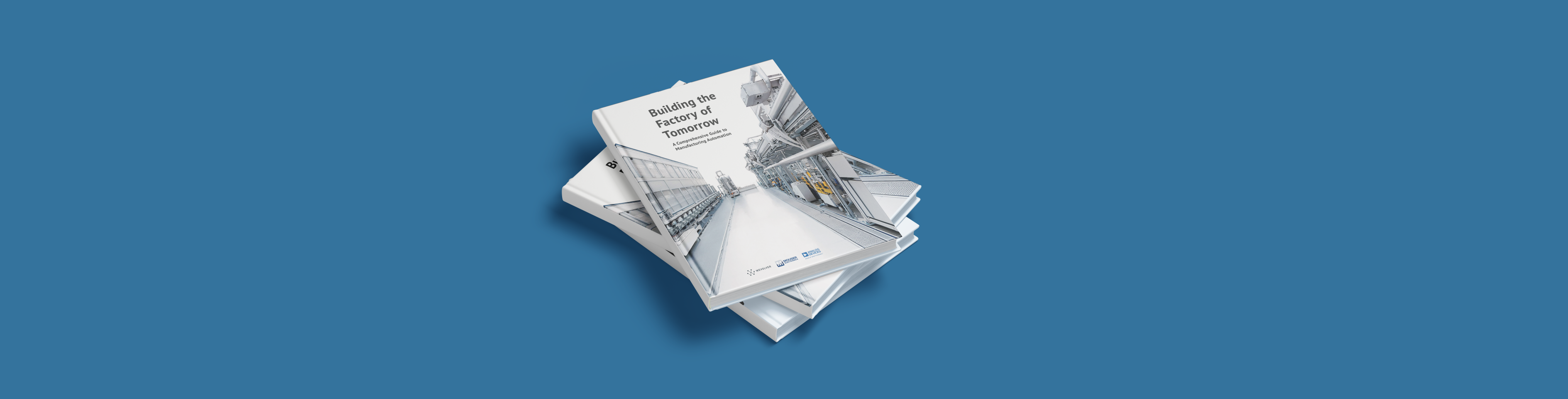
We will now discuss the human element of the modern factory. The ability of new factory technologies to work with humans on the factory floor is of utmost importance. Furthermore, the essential job duties of today’s factory workers will change, enabling higher-level decision-making via new skills. The workforce of modern factories must be provided with the necessary resources for training to develop a technologically proficient skill set.
The Human Factor in the Industry 5.0 Era
For every industrial revolution, the role of the factory worker has had to adapt.
First, during the Industry 1.0 and 2.0 eras, where steam and electricity respectively enabled machine operation, humans were required to operate and maintain all of the machinery, requiring labor-intensive, dangerous work. Computers spearheaded the Industry 3.0 revolution, in which the control of factory equipment became digitized, requiring factory workers to be proficient in assessing the performance of the machinery over a computer interface, allowing humans to slowly become more “hands-off” in the actual assembly line process. Lastly, the Industry 4.0 movement was predicated on increased connectivity and onboard intelligence via the Internet-of-Things market. The worker’s job shifted even further away from the fabrication process itself, and more into the monitoring and control of factory equipment based on the data obtained from each machine.
Now, in an Industry 5.0 factory, robotics and artificial intelligence (AI) take on the role of performing repetitive and dangerous manufacturing tasks, maximizing the efficiency and performance of the fabrication process. This will also minimize system downtime due to the ability to constantly operate via automated machines. However, due to this, the responsibility of the human factory worker will need to shift.
The role of humans will shift towards more cerebral activities, such as monitoring and diagnosing system performance via the data given by the thousands of sensors on the manufacturing floor. Furthermore, they must make decisions affecting the operation of the system components via a myriad of actuators. A welcome result of this will be the possibility of re-shoring previously offshored factory jobs, as the more advanced job responsibilities will lower the amount of total required workers while also requiring investment into well-trained and competent workers, enabling it as a desirable and competitive job market.
While many decisions will be made by people via data analytics and AI results, robotics within the manufacturing process will be able to make autonomous decisions due to intelligence at the edge, known as edge computing. The ability of these machines to make autonomous decisions that are critical to safety, reliability, and system performance must be trustworthy. The importance of network security is thus vital in the modern industrial process to ensure that these machines are making decisions based on reliable and accurate data, rather than anything malicious due to some sort of malware attack. The ability of trustworthy interactions at the human-to-machine interface is vital, as the hierarchy of decision-making of the process requires machines to make quick low-level decisions autonomously, while humans will make more top-level decisions.
To perform these tasks, factory workers must employ a new skill set, one in which they can understand and analyze substantial amounts of data and be able to make decisions in real-time. Furthermore, to effectively communicate and train tools within the factory system, they must be able to understand the concepts of AI. This ability to leverage the high amounts of data provided by sensors along the factory floor with the AI software that aids in decision-making is vital in order to confirm that autonomous machine decisions will operate correctly or if any human intervention is required due to the health of a specific machine, or the occurrence of some kind of unique situation.
AI can thus aid in real-time decision-making, which is critical to the minimization of system downtime, resulting in a fast-paced ever-changing work environment in which workers need to adapt to new situations based on the data coming in from the wealth of sensors and AI systems on the factory floor. This demonstrates that, as robotics technology makes its way to the factory floor, human workers must be able to properly and efficiently work alongside these automated machines in a safe manner. The importance of trustworthy decision-making by both machines and human workers is paramount to this, as the two must be able to perform their respective jobs and each make quality decisions to ensure proper operation.
As we are in the age of the Industry 5.0 revolution, the experience of the modern factory worker is taking a dramatic shift. Moving from the assembly line to the monitoring, diagnosis, and maintenance of the overall system requires new skills and essential job duties. These new skills are paired with a trustful relationship with the robotics along the manufacturing line to enable efficient and safe factory operation.
Understanding the Skills Gap
As previously stated, the job requirements of the modern factory worker are much different than previously, where the ability to handle big data and AI interfaces is paramount. Thus, there exists a skills gap that must be overcome.
According to the World Economic Forum, 44% of workers will need to learn new skills due to changing job requirements based on technological advancements. Some of these top skills align very well with the needs of the future factory worker. Such skills include analytical and critical thinking, technological literacy, dependability and attention to detail, AI and big data, systems thinking, and quality control. Some of these skills relate to the job of the earlier factory worker, but the onset of the digital manufacturing revolution requires many new skills that are currently not provided to these workers.
These new skills are due to the worker’s responsibility to observe manufacturing operations via the analysis of large amounts of data along with the aid of AI models, as well as the ability to observe and intervene as needed in the autonomous decision-making of the robotics used along the assembly line. Now, according to the World Manufacturing Forum Economic Report, companies need to prioritize the training of their workforce in order to master these new required skills.
Technological literacy is one of the most important tools within the modern factory worker’s tool belt. The work of manufacturing is moving from hands-on work at the assembly line to technical support and literacy via software tools. Here, the worker will analyze the manufacturing process, while ensuring proper network connectivity and security within the system. These essential job responsibilities require that workers be proficient in the communication and control systems that interconnect the machines on the factory floor. These skills need to be properly paired with advanced critical and analytical thinking capabilities. With the understanding of the systems used within the manufacturing process, workers must also be able to make informed and well-thought-out decisions in real-time based on the performance of these systems. This real-time capability is particularly important to minimize system downtime, thus maximizing efficiency and throughput.
AI and big data are one of the top skills of interest in this kind of field. This topic is within the top three priorities of companies in terms of hiring requirements and being a primary requirement for large companies (50,000 or more). It seems further that companies believe that the importance of AI and big data is not only a hot topic in today’s job market but will only grow in importance for future markets. The modern factory will not merely require workers to understand the basics of big data and AI, but in some cases, their jobs will shift to mainly a job that requires the analysis of large amounts of data as well as the usage and management of AI software tools in order to understand operation across the factory floor and make decisions accordingly.
These technical skills, while important to the essential responsibilities of modern factory workers, are still to be coupled with advanced soft skills. The ability to perform flexible and agile work, pay attention to detail, communicate effectively, and work well within a team is vital to success as well. These skills can also be improved via online course material and cannot be underestimated by companies in today’s market. Real-time decision-making is crucial to cutting downtime as much as possible. For this to happen, workers must be able to communicate and report on highly technical subjects in an efficient way so correct decisions can be made accordingly.
These decisions must also be made on complex and substantial amounts of data produced by sensors within the factory, and thus attention to detail is vital. While the usage of AI tools can help aid in decision making, workers must be able to confirm that the AI-based decisions are indeed accurate and thus will need to understand the raw generated data, which is abundant. Based on these communications, constant system maintenance and upkeep are needed, with different systems constantly requiring attention, leading to changing tasks constantly.
Overall, the skills of the modern-day factory worker are diverse and much different than what was previously needed. Thus, the ability of companies to close the skills gap between their employees and the skills that are needed for AI-enabled and data-driven manufacturing is essential for survival in today’s market and is an area in which investment in the education of their employees must be put as a top priority due to the lack of ability of all to have access to these resources, albeit online, due to their cost.
Filling the Skills Gap
Noting now that there is a skills gap for the factory workers of today to overcome, the question of how this can happen is next. The availability of content allows employees to learn the concepts of new skills, such as big data analysis, network communication and security protocols, and AI. Beyond these concepts, the application-specific nature of their work regarding these concepts, based on the machines and systems being utilized, must be taught as well.
While allowing workers to enhance their abilities based on these skills, a term more properly known as “upskilling” or “reskilling”, is a very important task that companies need to undergo in order to get ahead in the modern manufacturing market, it is an opportunity that approximately only half of workers will be able to receive the proper resources for upskilling, according to the World Economic Forum. This condition is currently changing, however, as online training websites, like Coursera, are providing access to quality online education content with the ability for users to obtain certificates of course completion, as well as legitimate collegiate certificates and degrees. Sites like these are especially great for upskilling for technology-related fields, offering course topics such as AI, big data, and general technical literacy, but also have courses relating to the required soft skills of the modern-day factory worker. These topics further have course options ranging from beginner to advanced difficulties, lending themselves to anybody, regardless of earlier experience. These courses also come in either guided or self-paced formats, allowing users to find the type of learning that best fits their needs and lifestyle.
While the ability to take these courses online enables many to take advantage of them regardless of geographical location, these courses however may be unable to be afforded by some. Due to this, for companies to get a competitive edge, funding education opportunities through companies like Coursera is vital to ensure a capable workforce. It has also been seen that skill-specific resources like this do not require advanced degrees to complete the requisite coursework in a reasonable time, as it was seen by a World Economic Forum Report on Jobs in 2023 that the required time was just about the same for all users, regardless on if those users had graduate degrees, or only undergraduate degrees, or neither of the two. This allows people of all educational backgrounds to become highly skilled workers in modern-day factories at all levels if given the proper on-the-job training.
These resources can further be paired with industry and tool-specific training which is offered by a variety of hardware devices, tools, and software companies. Like Coursera, some of these can be offered as self-paced online classes, while others can be on-site training given to employees. These can supplement theoretical and general training with application-specific content that will allow employees to not only understand the system as a whole but also be able to aptly utilize all of the specific tools at their disposal, allowing them to readily diagnose any issues and maximize the efficiency of the manufacturing process. On-the-job training also does not have to be given by an outside entity, but the company itself would require a proper training program for onboarding employees, or employees who are transitioning to new roles. These are ideal as they are highly specific to the specific job of the employee, which is the best way to ensure that each worker understands how to properly interact.
Utilizing a proper mix of theoretical, tool-based, and job-specific training, the modern factory worker can undergo the proper upskilling and reskilling requirements to meet the needs of the advanced factories of today. This is a critical need for companies to make, requiring their investment to ensure that the proper content is accessed by employees across the board. Ensuring the access that employees have to these resources will ensure that the skills gap of workers in the industry today can be closed as much as possible.
Case Studies
After discussing all of the requirements of the modern-day factory and how companies can help meet these, we will look into how these have been implemented in reality and the payout that was seen due to following the needs illustrated in this chapter.
For example, consider the experience of Sandra Jaksic of the Chalmers University of Technology, who discusses how the rework of a company’s business model based on three fundamental shifts resulted in huge payouts for the company.
The first shift was defined as the service shift. This movement illustrates how manufacturing companies are moving from a product-centric focus to a service-centric focus. An example illustrating this shift is how Rolls-Royce shifted from selling manufactured jet engines to starting a “power by the hour” service offering a fixed-price maintenance plan for customers using their engines. This was due to a loss in revenue as data analytics helped dramatically improve jet engine lifetime, leading to a decrease in sales. This shift creates a need for increased customer engagement, requiring factory workers to engage with outside customers on a normal basis, as opposed to the earlier ideology where they focused on only what was made internally and just sent it out.
The second shift is the digital shift. This denotes the introduction of digital systems such as AI, digital twins, Internet-of-Things (IoT) connectivity, and big data into the manufacturing process. The use of these digital systems, as we have discussed previously, increases manufacturing throughput and product quality. An example of this can be seen by Siemens Electronics Works Amberg (EWA) which has been propelled to the top of the technology manufacturing market via their inclusion of digital intelligence into 75% of their processes. Due to this, over 14 years, they see a daily product quality of 99.9999% achieved consistently, maximizing product throughput. Furthermore, since 1990, a 14-fold increase in productivity and a 140% increase in factory output has been seen because these systems can operate autonomously when needed, minimizing downtime. This behavior has been seen even as more complex products have been incorporated into the production line. This shift also allows employees to use their time to perform more thought-intensive work that allows them to utilize data obtained from the factory floor to make real-time decisions, allowing for system performance to stay at a high value.
The final shift, known as the circular shift, again shifts the aim of a production company to act as a service provider, as they transition from a linear production model to a circular one in which products that reach the end of their lifetime are reused and/or recycled. This requires that employees collaborate with customers as they prioritize the maintenance and repair of customer products. IKEA gives a fitting example of how this has been implemented.
Emphasizing green technology, they have changed how their products are built, by getting rid of fasteners such as nails and screws and replacing them with hardware that allows users to take apart and repair pieces of the furniture bought rather than requiring a whole new piece. A mattress recycling program has also been implemented for the repurposing of old mattresses rather than being discarded. This requires that factory workers be able to adapt the process of the factory floor based on whether it is being used to produce new products or the repurposing of the old. Workers adapting robotics along the floor rather than having humans change their work helps to make this change quicker, minimizing downtime.
Here, we see how the modern factory worker plays a vital role in the new business models seen by manufacturing companies, and how their ability to adapt to new skills and new workflows is paramount to the company’s success.
Overall, in the scope of the development of modern factories, industrial solution providers and manufacturing enterprises tend to focus most of the time on the advanced technologies that they deploy, often forgetting the human element behind them. Nevertheless, the operation of the factories of the future is not possible without properly skilled workers and without investments in human-centric technologies that are accepted by workers. The workers behind the machines and the digital technologies of the factories of the future must be able to change the way that they work drastically, learning new skills and enhancing already known ones. Therefore, manufacturing enterprises have no other option than to invest in the reskilling and upskilling of their workers, while at the same time ensuring that the deployed technologies are robust, resilient, and trusted by humans.
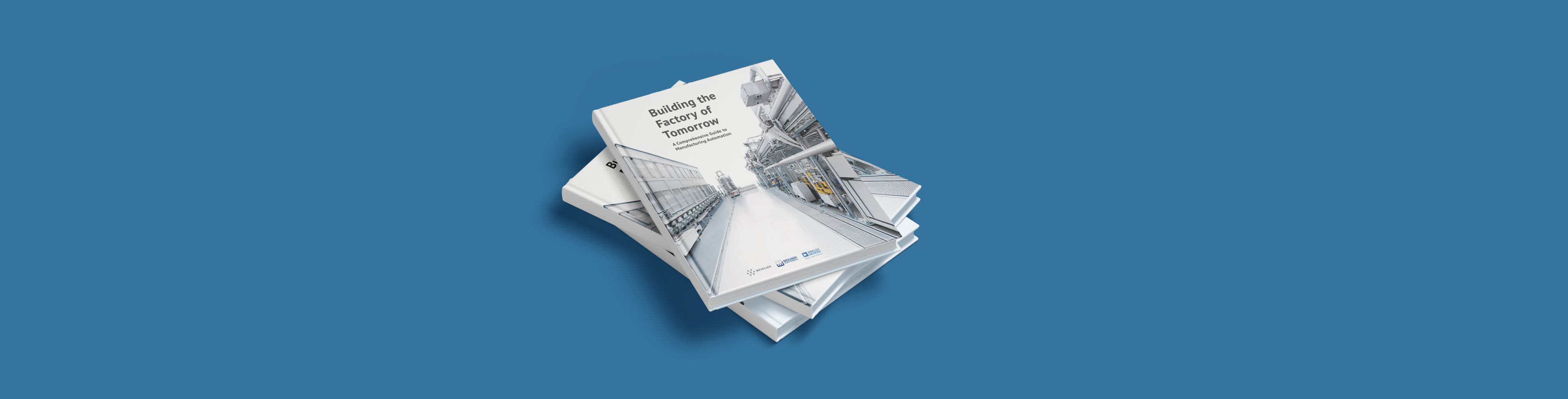