Our latest report, Building the Factory of Tomorrow, offers an in-depth analysis of the core forces shaping modern industrial production, from the accelerated pace of technological innovation to the integration of human-robot collaboration in next-generation factories.
Download this detailed report to explore:
- Cutting-edge advancements in AI, Quantum Computing, and Hyper Automation that are impacting manufacturing processes.
- The impact of globalized supply chains and virtual collaboration tools in enabling seamless cross-border operations.
- The shift toward sustainable production models, emphasizing circular value chains and carbon-neutral practices.
This report provides valuable technical insights for engineers, industry leaders, and decision-makers seeking to leverage the latest innovations and strategic trends to enhance operational efficiency and remain competitive in a rapidly changing landscape.
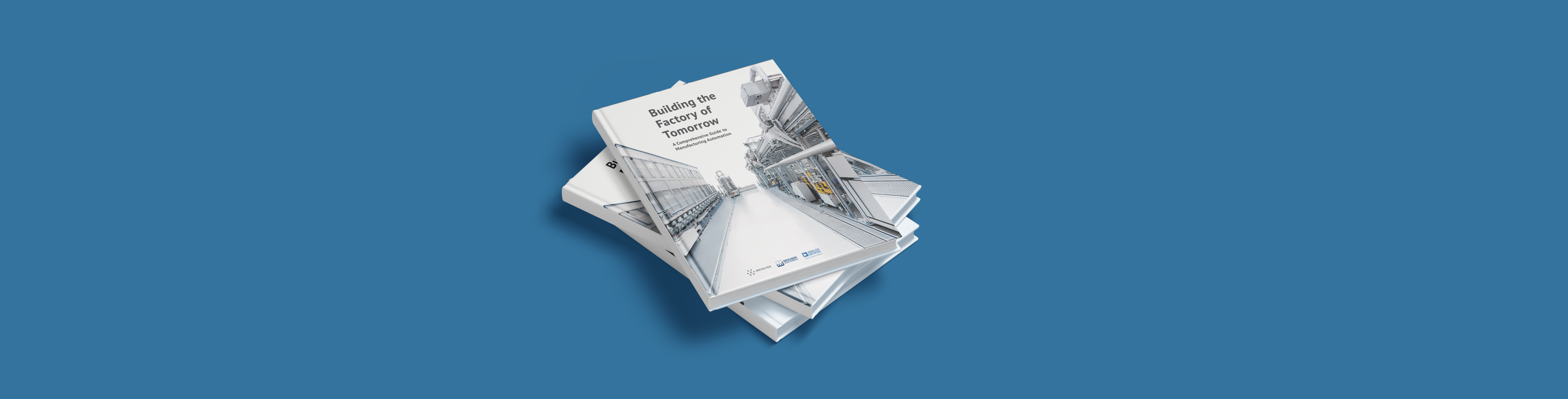
The factories of the future will comprise cutting-edge technologies that will enable the digitization of their operations based on a convergence between the physical and digital worlds. Industry 4.0 and Industry 5.0 are largely about the effective deployment of non-trivial cyber-physical production systems on the manufacturing shop floor and across the manufacturing value chain. The latter must be supported by a host of different technologies for collecting and analysing digital data, while at the same time using them in use cases like quality control, predictive maintenance, and what-if simulations based on digital twins. In this context, the construction of future factories requires a very good understanding of future digital technologies that will serve as “digital enablers' and catalysts for an effective digital transformation of production processes.
Broadband Networks 5G/6G
The Evolution of Networking towards 5G
Recent advances in networking technologies are already reshaping the ways factories operate. Among these advancements, the emergence of 5G and the promise of 6G networks hold significant potential for powering the factories of the future. To understand the benefits of these technologies for state-of-the-art and for future industrial applications, it’s always worth exploring the evolution of networking from 1G to 6G in terms of the value-added characteristics and functionalities of each generation of telecommunications.
The journey from the first generation (1G) of mobile communication to the upcoming sixth generation (6G) has been marked by tremendous advancements and transformative capabilities. 1G, introduced in the 1980s, offered antilog voice communication. Subsequent generations, 2G, 3G, and 4G, brought digital voice communication, data services, and broadband connectivity, respectively. These developments laid the foundation for the current state of connectivity, where the integration of higher data rates, lower latency, increased capacity, and unprecedented flexibility has become essential.
Understanding 5G’s Potential
5G networks represent a significant leap forward in wireless communication, enabling faster data transmission, lower latency, and higher device density. In terms of networking speed, 5G networks can increase download speeds tenfold when compared to 4G networks. At the same time, 5G networks are designed to support dense IoT environments, as they can connect a significantly higher number of devices per unit area than previous generations. Moreover, 5G ensures seamless communication among numerous IoT devices simultaneously. The reduced latency of 5G networks enables real-time interactions between IoT devices, which allows for faster response times and improved overall performance in crowded IoT environments. This enables the smooth functioning of IoT applications even in IoT-dense environments such as industrial plants with thousands of sensors and IoT devices.
The flexibility of 5G is another key advantage for future factories. One notable feature of 5G networking in this direction is network slicing, which allows the division of a single physical network into multiple virtual networks tailored to different industrial applications. In a factory setting, this implies the ability to allocate dedicated network slices with varying characteristics for different use cases, such as real-time control systems, autonomous vehicles, and massive sensor networks. This flexibility enhances overall system efficiency while ensuring uninterrupted connectivity and reliable performance for critical applications.
Most importantly, it is nowadays possible to develop private 5G networking infrastructures that are tailored to the requirements of production operations. Specifically, private 5G networks provide manufacturing enterprises with the ability to establish their own localized, secure, and high-performance communication infrastructure. This offers several advantages such as real-time data exchange and processes in support of low latency use cases such as near real-time detection of defects.
It also enables rapid decision-making that leads to improved operational efficiency. Moreover, private 5G networks provide increased privacy, security, and data protection, as they obviate the need for manufacturers to rely on public networking infrastructures and services. Security and data protection are crucial concerns in manufacturing settings where proprietary information, intellectual property (IP), and trade secrets are very often exchanged. Private 5G networks can benefit from slicing mechanisms to deliver exceptional flexibility and configurability that meets modern manufacturers’ needs.
An integral component of most 5G deployments is a TSN (Time-Sensitive Network) part, which offers low latency features over industrial ethernet infrastructures. The integration of TSN modules within a 5G network will be a key enabler of Quality of Service, reliability, and configurability functionalities within the future factories.
Factory-5G use-cases in a converged industrial network.
Unlocking Future Possibilities with Emerging 6G Infrastructures
While 5G networks are still being rolled out worldwide, the anticipation for 6G is already building. 6G aims to take connectivity and capabilities to unprecedented levels, with expectations of data rates reaching 100 times faster than 5G. In particular, 6G networks are expected to be the successor to 5G networks, with even faster speeds, lower latencies, and expanded capabilities. For instance, while 5G aims to provide download speeds up to 10 Gbps, 6G is projected to achieve speeds of up to 100 Gbps. 6G is also expected to support advanced technologies and applications like holographic communication, AI integration, and immersive experiences.
The 6G next-generation networking technology could revolutionize numerous industries, including manufacturing, which makes it a perfect candidate for the future factories. With ultra-low latency and massive data-handling capabilities, 6G will enable real-time decision-making, facilitating faster response times and enhancing automation in factories. Moreover, advanced features such as holographic communication, distributed sensing, and AI-driven intelligence are expected to enable more advanced and immersive experiences, like Extended Reality (XR) based applications for industrial training and remote maintenance.
5G/6G and TSN Importance for Manufacturing Use Cases
5G/6G networks will bring about transformative changes in industrial applications. They will enable real-time edge computing that will enable immediate data analysis and processing at the edge of the network, near the source of data generation. Moreover, the integration of TSN modules will provide support for ultra-low-latency application scenarios. These capabilities will be instrumental for many emerging manufacturing use cases where quick decision-making is required, such as:
Predictive maintenance: In the context of predictive maintenance, sensors and devices embedded in machines can transmit real-time data to edge computing systems. Analysing this data in real-time enables the detection of potential issues before they escalate, preventing costly downtime and enhancing operational efficiency.
Quality control: Quality control can also benefit from real-time edge computing, where data from sensors and cameras can be analysed on the spot, ensuring product quality, and reducing waste as problems will be spotted and remedied before they materialise on the shopfloor.
Supply chain optimization: 5G/6G networks enable real-time monitoring of supply chain operations through extensive deployment of sensors and IoT devices. Leveraging the ability to transmit large volumes of data rapidly, manufacturers will gain real-time visibility into their supply chain. This will help the factories of the future to optimize inventory management, predict demand fluctuations, and improve overall logistics efficiency.
Cloud/Edge Computing
Benefits and Limitations of Cloud Computing
The cloud computing model refers to accessing computing resources (e.g., compute capacity, storage, software) from a remote (rather than a local on premise) data centre. Access to such resources is performed in an elastic fashion i.e., more resources are saleably available whenever needed. Most importantly, in a cloud computing model users pay for what they use. For over fifteen years, cloud computing models have transformed the ways industrial enterprise access and use computing services through offering unprecedented scalability, capacity, and Quality of Service (QoS).
In the manufacturing space, cloud computing offers manufacturers a plethora of advantages that fundamentally transform operational dynamics. Relevant benefits include flexibility, seamless scalability of resources in response to fluctuating demands, elasticity, allowing for dynamic resource provisioning to optimize efficiency, cost control, as well as minimization of upfront infrastructure investments, interoperability, and easier integration across diverse systems and applications. Most importantly, cloud computing is an enabler of novel manufacturing business models and paradigms such as Manufacturing as a Service (MaaS), which provides on-demand access to servitized manufacturing capabilities such as physical assets (e.g., 3D printers, machinery) and supply chain management functions. Likewise, it has also enabled novel manufacturing approaches such as Asset-as-a-Service, which provides flexible, on-demand access to machining capabilities.
Nevertheless, despite its transformative potential, cloud computing also presents limitations that impact manufacturing operations. As a prominent example, MaaS models are usually characterized by high latency, which is a result of data transmission to and from remote servers. High latency can hinder real-time responsiveness, which is critical in various manufacturing processes. Another disadvantage of cloud manufacturing is its poor energy efficiency: data centre operations consume substantial power resources. This poses environmental concerns and operational overheads, which is a setback to achieving the ambitious environmental performance targets of the Industry 5.0 era. Furthermore, cloud-based manufacturing operations can face data security and protection issues, which arise from the reliance on third-party cloud service providers. This necessitates robust measures to safeguard sensitive manufacturing data from breaches and unauthorized access.
Edge Computing for Manufacturing Use Cases
To alleviate the limitations and disadvantages of cloud computing, industrial enterprises are nowadays extending their computational capabilities to the edge of the network i.e., closer to data sources and endpoints. This approach addresses the constraints of centralized cloud infrastructure, as selected computing resources and functions are made accessible close to the manufacturing data sources and devices. Specifically, edge computing alleviates latency issues by enabling real-time data processing and analysis at the edge. Hence, edge computing empowers factories to deploy localized computing resources for time-sensitive applications, which enhances operational responsiveness and efficiency.
In manufacturing use cases, edge computing manifests through various functionalities tailored to optimized production processes. Real-time predictive maintenance stands out as a prominent use case, where sensors such as the ADI OtoSense Smart Motor Sensor are embedded in machinery to capture data that is processed locally at the edge to pre-emptively identify equipment anomalies and prevent breakdowns. This can also greatly improve the speed and effectiveness of defect detection and quality control functions.
Moreover, edge analytics (i.e., analysing manufacturing data at the edge) through devices such as Voyager 3 Wireless Vibration Monitoring Platform enables real-time monitoring of machine performance, quality control, and inventory management. The latter functions foster agile decision-making and operational excellence on the shopfloor. Most importantly, edge computing functions improve the power-efficiency of manufacturing functions, by minimizing data transfers from/to remote clouds. Data can be processed locally and only selected analytics outcomes (e.g., manufacturing events and insights) can be communicated to the remote cloud.
Cloud and Edge Computing Inter-Play for Effective Manufacturing Processes
In practice, cloud and edge functions are combined in the scope of manufacturing use cases. Edge functions deliver real-time performance and energy-efficient operations, while cloud functions provide the capacity needed to process large numbers of data points and the versatility needed for sharing data with other actors in the manufacturing chain. Overall, while the cloud remains instrumental for centralized data storage, complex analytics, and non-real-time applications that do not demand immediate processing, edge computing excels in time-sensitive tasks requiring local processing, such as real-time monitoring, control systems, and edge analytics at the production line. Therefore, the strategic allocation of functions between cloud and edge computing is paramount in maximizing operational efficacy in manufacturing environments.
The optimal interplay between cloud and edge computing architectures manifests in a hybrid approach, where data is processed and stored both centrally in the cloud for historical analysis and locally at the edge for real-time decision-making. By delineating functions based on latency, bandwidth requirements, and data sensitivity, manufacturers can harness the synergistic capabilities of cloud and edge computing to streamline operations, improve productivity, and drive innovation. Overall, future factories must offer and effectively combine both cloud computing and edge computing capabilities.
Data optimization for smart quality management empowered by edge computing from Industry 5.0 perspective.
Internet of Things and Cyber-Physical Systems
Introducing the Industrial Internet of Things
The Internet of Things (IoT) embodies a network of interconnected devices, sensors, and systems that communicate and share data. It enables the collection and analysis of real-time information, as well as the execution of physical operations in industrial environments like manufacturing shop floors, energy plants and gigafactories. In the manufacturing sector, IoT deployments fall in the realm of the so-called Industrial Internet of Things (IIoT), which focuses on industrial rather than consumer-related devices and processes. Specifically, IIoT deployments in the manufacturing sector focus on the interconnection of machines, equipment, and processes towards optimizing productivity, efficiency, and resource allocation.
Closely intertwined with IoT is the concept of Cyber-Physical Systems (CPS), which represents the integration of physical processes with digital technology. CPS operates through a combination of sensors, actuators, and computational systems that monitor and control physical processes in real-time. This integration enables the interaction of the physical and digital worlds, which facilitates autonomous decision-making and adaptable manufacturing systems. CPS systems are considered as the key enabler of Industry 4.0 systems and applications that end-up blurring the boundaries of the physical and digital worlds in industrial environments.
IIoT in Manufacturing: Empowering Cyber-Physical Production Systems (CPPS)
One of the primary benefits offered by IoT and CPS in manufacturing is the digitization of physical processes. Traditionally, manufacturing operations were reliant on manual monitoring and control mechanisms. With IoT and CPS, physical processes can be equipped with sensors, enabling real-time data acquisition and analysis as part of a convergence of Operational Technology (OT) (e.g., automation devices) with Information Technology (IT). This convergence lays the groundwork for a variety of digitally enabled production processes.
IoT-enabled automation devices play a pivotal role in the implementation of IoT and CPS in manufacturing. Prominent examples of such devices include robots, autonomous drones, wearable technologies, and smart sensors. In the scope of IIoT deployments, these devices can work cohesively to gather data, communicate, and execute tasks autonomously. Through IIoT, future factories will be able to leverage real-time data analytics, machine learning algorithms, and artificial intelligence to optimize production processes, support predictive maintenance programs, and enable adaptive manufacturing.
Industry 4.0 and Industry 5.0 factories will implement a novel integration of IIoT and CPS systems, which will result in Cyber-Physical Production Systems (CPPS). In the scope of CPPS systems physical processes will be closely interconnected with digital systems to create highly adaptable and intelligent production environments. CPPS systems will be deployed in various cloud/edge computing configurations forming an integrated computing continuum that transcends cloud data centres, edge clusters, as well as IoT devices.
CPPS framework.
Understanding IIoT challenges in future factories
The integration of thousands of IoT-connected devices in future factories will come not only with operational benefits, but also with a host of different challenges that industrial enterprises will have to address. One of the primary challenges is establishing trust and ensuring the security of IoT devices and CPS within industrial environments. The sheer number of connected devices increases the attack surface, making factories susceptible to cyber threats. Safeguarding against malicious actors and unauthorized access becomes important towards protecting critical infrastructures, sensitive data, and maintaining operational continuity. Devices like the ADIN2299 Multiprotocol -Port Industrial Ethernet Platform can help by providing secure, real-time industrial Ethernet communication, ensuring network integrity and reducing vulnerabilities. Implementing robust security measures, such as encryption, authentication protocols, access controls, and continuous monitoring, can mitigate these risks.
Efficient data management poses another challenge for manufacturers that adopt IIoT. The volume of data generated by IoT and CPS devices in the factories of the future can quickly become overwhelming. Therefore, extracting meaningful insights from this data requires proper storage, analysis, and retrieval mechanisms. The MAX32672 Ultra-Low Power ARM Cortex-M4F Microcontroller provides an energy-efficient processing platform for real-time data analysis, helping manufacturers manage large amounts of data while keeping power consumption low. Furthermore, ensuring data integrity and privacy is essential to avoid unauthorized access and potential data breaches. The ADP1034 Micropower Management Unit can assist in efficient power management for IoT devices, ensuring stable and secure operation, which is crucial for maintaining data integrity. To this end, manufacturers must employ data management frameworks that ensure data quality, interoperability, and access control.
Device certification is one more crucial aspect of deploying IoT devices and CPS in factories. Devices must conform to industry standards and security best practices in order to guarantee their reliability and compatibility within the ecosystem where they are deployed. Failure to adequately certify devices can result in interoperability issues, compromise system integrity, or lead to operational inefficiencies. Nowadays, the lack of certification is one of the main reasons why manufacturers are currently reluctant to deploy large numbers of novel IoT devices in their factories. The AD74115H Industrial I/O Device offers robust performance in harsh industrial environments, ensures compliance with strict industry standards, contributing to system reliability.
Note also that the deployment of IoT devices and CPS necessitates overcoming compatibility challenges between legacy systems and newer technologies. Ensuring seamless integration and communication between heterogeneous systems requires systematic planning and significant upfront investments. Downstream challenges can arise from the complexities of retrofitting existing infrastructure with IoT-enabled devices and CPS, which can also hinder the adoption of these technologies. Devices like the MAX20075 Buck Converter, which provides efficient power conversion, and the MAX17523A Current Limiter, which protects devices from power surges, can help ensure smooth integration of newer technologies into legacy systems.
Big Data Management
The 4Vs of Big Data in a Manufacturing Context
Nowadays manufacturers harness and analyse large and diverse datasets to unveil valuable insights and gain a competitive edge. As data generation grows future factories will have to implement and deploy scalable and cost-effective infrastructures for managing them.
Big Data is characterized by its four Vs: Volume, Velocity, Variety, and Veracity:
Volume, which refers to the vast amount of data generated and collected by manufacturing systems. In modern factories, numerous sensors, IoT devices, and operational systems continuously generate massive volumes of data. For instance, in predictive maintenance applications, sensor data from machinery and equipment are collected and analysed to predict failures and optimize maintenance schedules. As another example, customer data, supply chain data, and product performance data contribute to the volume of data generated in manufacturing.
Velocity, which represents the speed at which data is created and processed. Future factories comprise data sources (e.g., sensors) that produce data with very high ingestion rates. The real-time processing and analysis of such data are crucial to enhance operational efficiency and respond to dynamic conditions.
Variety, which refers to the diverse types of data generated in manufacturing. Specifically, manufacturing systems generate structured data from databases, ERP systems, and automation devices such as Programmable Logic Controllers (PLCs) and Distributed Control Systems (DCS), as well as unstructured data from images, videos, and text. Combining and analysing this diverse data can provide valuable insights for manufacturing use cases. For instance, product images can be analysed along with product specifications to spot quality control problems.
Veracity, which is about the quality and reliability of the data. In manufacturing, data integrity and accuracy are critical for making informed decisions. Nevertheless, data may be subject to various sources of noise and inconsistencies, such as sensor inaccuracies or communication errors. To alleviate these issues, Big Data systems implement various data cleansing and validation techniques to ensure that the data used for analysis is reliable and trustworthy.
Data with the above-listed properties cannot be typically handled by conventional databases, which is the reason why Big Data systems and Big Data databases have emerged. The latter are increasingly part of the data management infrastructures of modern factories.
Data Management Infrastructures in Future Factories
To effectively manage and analyse Big Data in manufacturing, advanced data infrastructures are required, including conventional data management infrastructure and Big Data systems. Traditional databases and data warehouses are still valuable for structured data storage and analysis. Furthermore, historians i.e., specialized databases designed for time-series data, remain important and relevant towards capturing and analysing operational data over time. However, the increasing volume and variety of data have driven the adoption of new technologies like Big Data databases and NoSQL databases.
Big Data databases are designed to handle large volumes of diverse data types, providing scalability and fault tolerance. They enable distributed storage and parallel processing, which allows providers of industrial automation solutions to efficiently handle and analyse Big Data. On the other hand, NoSQL databases are well-suited for unstructured data. These data infrastructures facilitate the storage, retrieval, and analysis of Big Data, enabling manufacturers to make data-driven decisions and gain insights at scale.
Big Data is one of the foundational elements for building effective Machine Learning (ML) and Artificial Intelligence (AI) systems in manufacturing. AI systems depend on vast amounts of high-quality data for learning and making intelligent decisions.
The 4Vs of Big Data play a crucial role in training effective AI/ML systems towards driving successful AI adoption. Specifically, the volume of data allows AI systems to learn from diverse examples and adapt to various scenarios. For example, in predictive maintenance, AI algorithms can learn from large volumes of historic sensor data to identify patterns indicative of impending machine failures. As already outlined, the velocity of data ensures that AI systems can operate in real-time towards providing immediate response and decision-making capabilities. Also, the variety of data provides AI systems with a comprehensive understanding of manufacturing operations. Based on a combination of structured and unstructured data sources, AI algorithms can uncover hidden patterns and correlations that were previously unseen. Finally, the veracity of data ensures that AI systems are built on reliable and trustworthy information.
Machine Learning
Different Types of ML Models and Paradigms for Manufacturing Use Cases
In the context of manufacturing, Machine Learning (ML) is a powerful subset of Artificial Intelligence (AI) that offers tremendous potential for process optimization, quality control, predictive maintenance, and other critical areas. There are many different types of machine learning models and systems, which are useful and relevant for industrial production use cases.
As a prominent example, classical Machine Learning refers to the traditional methods and algorithms used for pattern recognition and prediction, including models like decision trees, random forests, linear regression, logistic regression, neural networks and many more. In manufacturing, such classical ML techniques play a significant role in areas such as fault detection, anomaly detection, and predictive maintenance. For instance, classical ML models can be trained on historical data to help manufacturers predict machine failures in advance, identify quality issues, and optimize production processes.
While classical ML models represent the majority of the ML models available, for over a decade there has been increased emphasis on a smaller subset of ML models, namely deep learning models. Deep Learning is a subset of ML that focuses on training artificial neural networks with many neurons structured in many layers. The growing interest in deep neural networks stems from their ability to continually improve their performance as more training data become available. This is not the case with classical ML models, which tend to reach a performance plateau when training with a relatively small or moderate amount of data.
In an era where data generation has exploded, there are many opportunities for using deep learning models to improve ML performance. Hence, deep learning excels in handling complex data such as images, videos, and text, as part of use cases for tasks such as defect detection, visual inspection, and quality control. For instance, in the automotive industry, Deep Learning algorithms can be trained to analyse images of car body surfaces to detect and classify defects like scratches, dents, or paint irregularities. This enables automated inspection and improves overall product quality.
Apart from classical ML and deep learning, manufacturing use cases benefit from reinforcement learning models. Reinforcement Learning (RL) involves training an agent to interact with an environment in order to maximize a specific objective. Specifically, during the training process, RL agents are rewarded for proper actions and behaviours, and penalized for actions that fail to contribute to the target objective. For example, RL can be applied to optimize production schedules, energy consumption, and logistics. In the case of RL-based optimization of production line scheduling, an RL agent is trained to make decisions on job assignments, machine allocations, and sequencing. This helps manufacturers to improve throughput, reduce lead times, and minimize changeover costs. Most importantly, RL models are used for training industrial robots to move appropriately in the shopfloor.
Large Language Models in Manufacturing
During the last couple of years, the interest around Large Language Models (LLMs) is booming. Large Language Models (LLMs) are advanced artificial intelligence (AI) models that can generate human-like text and other multimedia (e.g., images, video, audio) by understanding and predicting patterns in natural language. They are trained on vast amounts of data and can understand and generate content in a contextually relevant and coherent manner.
Following the release of popular applications like ChatGPT and the significant increase of the size and capabilities of state-of-the-art LLMs (e.g., GPT-3, GPT-4, Claude, LLaMa2), LLMs are deployed in almost every industrial sector. The manufacturing industry is no exception to this trend, as LLMs have potential applications in various areas, such as human-centric interaction and supply chain optimization.
As a prominent example, LLMs can improve human-robot interaction by enabling more natural and intuitive communication between workers and machines. In this direction, LLMs can be used to develop chatbot interfaces that assist operators in troubleshooting machinery issues, providing real-time guidance and support, as well as in answering on-the-job queries. Such human-centric interactions can boost productivity and reduce downtime by empowering workers to communicate effectively with machines, even when they are not familiar with complex programming or technical details.
As another example, LLMs can be employed for supply chain optimization. In particular, they can be used to analyse a vast array of data sources towards improving decision-making. They can analyse customer sentiment from social media, sales reports, and news events, towards helping manufacturers to predict and anticipate demand in order to adapt their production schedules accordingly. LLMs can also be used to optimize inventory management by predicting fluctuations in demand, reducing waste, and minimizing stockouts. Also, it is possible to use LLMs to support risk assessment and mitigation processes based on suggestions of alternative suppliers and prediction potential supply chain disruptions.
Future factories will certainly benefit from LLMs reasoning abilities that will enable enhanced data analysis, trend prediction, and decision support. Nowadays, LLMs have several limitations as well, including for example risks of bias and inaccuracies. Such challenges need to be addressed based on careful curation of training data, monitoring, and explainability of the results. However, we are also seeing a gradual, but tangible improvement of LLM operations and outcomes, which means that some of the above-listed risks will be alleviated based on the evolution of LLM technology in the years to come.
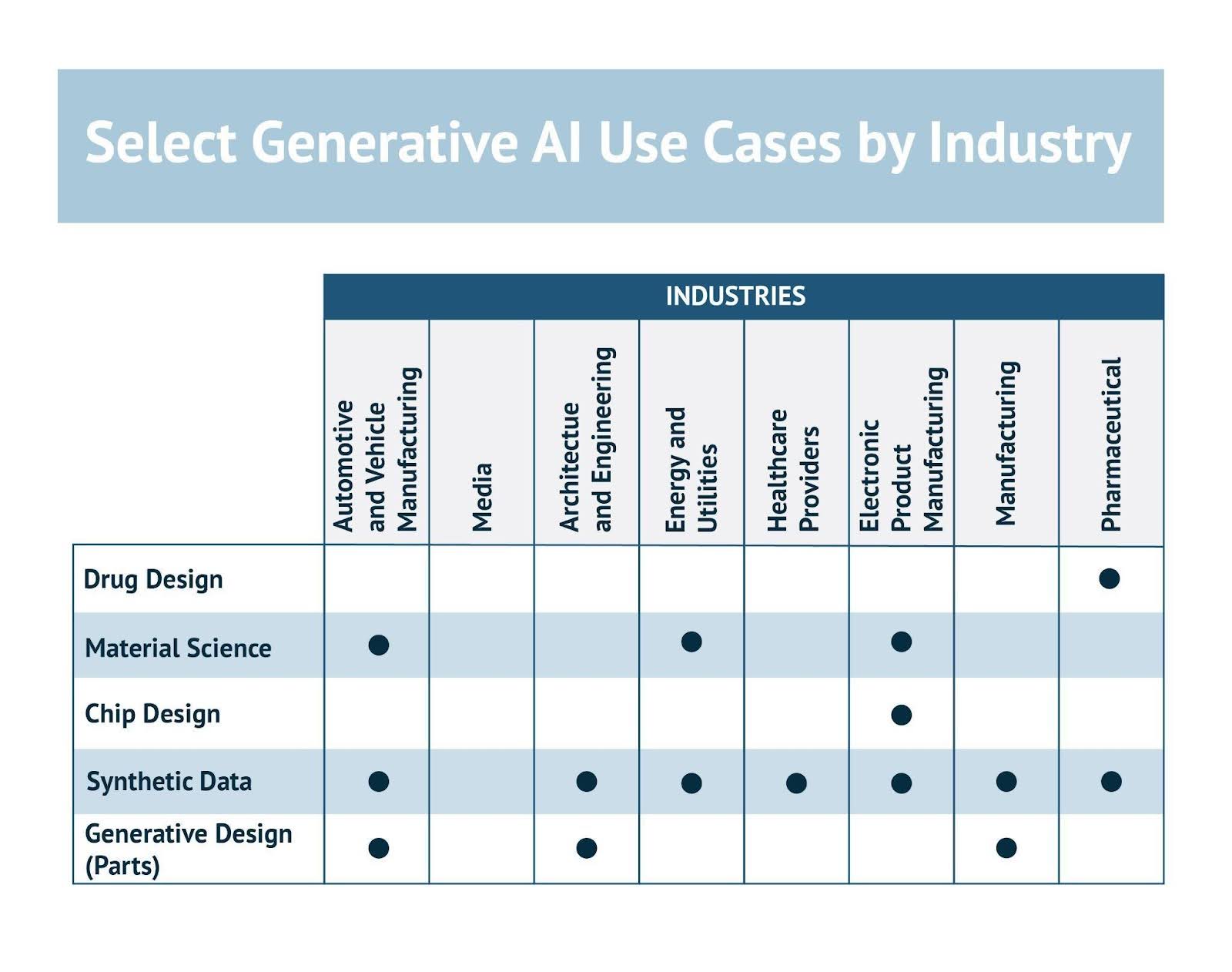
Deploying Models Close to the data sources: EdgeAI and TinyML
Nowadays, ML models for industrial use cases can be deployed and used in different cloud/edge computing configurations. Such deployments fall in the scope of EdgeAI approaches that blend ML models into edge computing deployments. Deploying machine learning models for manufacturing use cases close to the field (i.e., at the Edge), offers numerous advantages in terms of energy efficiency, low latency, and enhanced decision-making. Specifically, Edge AI approaches enable real-time processing of data directly at or near the source, which eliminates the need to send massive amounts of data to centralised cloud servers for analysis. This allows for quicker insights, faster response times, and reduced network congestion.
There are different approaches to implementing and deploying Edge AI systems. One of the most prominent approaches is Embedded Machine Learning (EML), which involves integrating ML models directly into devices or equipment at the Edge. In most cases lightweight models are embedded onto devices such as sensors, controllers, and machinery, to enable real-time data analysis and decision-making on-site. This approach minimizes the dependency on cloud connectivity and ensures that operations continue smoothly even in low or intermittent network conditions. A special case of embedded machine learning is TinyML. This refers to the deployment of ultra-low-power machine learning models on resource-constrained devices at the Edge, such as microcontrollers. TinyML optimizes models for minimal computational and memory requirements, which enables efficient data processing on devices with limited processing capabilities. This unlocks possibilities for a wide range of manufacturing use cases such as the detection of anomalies and defects based on tiny sensors embedded in the machinery.
Trustworthy and Explainable AI
Industry 5.0 emphasises the importance of trustworthy, human-centred interactions between workers and digitally-enabled production systems. In the case of AI-powered systems, the deployment and use of trustworthy AI technologies is very important to underpin proper human-robot and human-machine interactions. Specifically, the successful integration of AI into manufacturing operations relies on the trust and acceptance of AI outcomes by human workers and other manufacturing employees. Without trust in AI systems' decisions and actions, employees may resist working alongside these technologies, which is likely to hinder productivity and minimize efficiency gains. Therefore, ensuring the trustworthiness of AI is essential for fostering collaboration and achieving the full potential of Industry 5.0.
The development of trustworthy AI systems has many different dimensions, including for example safeguarding the security and integrity of the training data, auditing of the operation, and decisions of the system, as well as ensuring the use of robust AI models with reproducible results. One of the most important aspects of AI trustworthiness is the ability to explain the actions and decisions of AI systems. In this direction, future factories will integrate Explainable AI (XAI) technology, which plays a significant role in increasing the trustworthiness and transparency of AI models in manufacturing. XAI algorithms provide insights into how AI models arrive at their decisions, which boosts transparency and understandability of the AI decision making. AI explanations will be very important towards instilling confidence in users and help them better understand and trust the technology. For instance, XAI techniques will be used to explain to the worker why an AI system classified a product as defective, as well as why a specific production schedule was suggested by an AI-enabled recommendation engine.
Building Multi-Disciplinary Teams for Effective ML Systems in Manufacturing
The development of effective ML systems for manufacturing use cases is still a very challenging task that requires the involvement of multi-disciplinary teams. First and foremost, it requires the engagement of domain experts with a deep understanding of manufacturing processes and problems for successfully applying ML techniques. They provide insights into process dynamics, identify relevant variables, and help frame the problem in a meaningful way. Their expertise helps ensure that ML models and algorithms align with manufacturing goals and constraints. At the same time, the involvement of data scientists and ML experts is needed. These experts are responsible for data pre-processing, feature engineering, model selection, and optimization. They will also analyse the outputs of ML models to extract insights that can improve manufacturing processes and decision-making. Furthermore, data engineers must be engaged to undertake the tasks of efficiently collecting, storing, managing, and processing large volumes of data. They ensure data quality, data integration, and efficient data retrieval for ML training and analytics. In many cases, there is also a need for visualisation experts that develop ergonomic and user-friendly representations of AI insights and outcomes.
Overall, to adopt and fully leverage AI in their future factories, manufacturers will have to build and engage multi-disciplinary teams consisting of different experts, including the above-listed profile, as well as experts in legal, ethical, and regulatory aspects. This must be considered when planning the required cultural shift of industrial organizations towards the Industry 4.0 and Industry 5.0 era.
Industrial Robots and Cobots
Industrial robots are integral elements of modern manufacturing environments. They are used to automate a wide range of tasks in ways that improve efficiency, precision, and productivity. They are used in many different manufacturing processes, such as assembly, welding, painting, material handling, and quality control. One of the main advantages is that they can operate 24/7 towards delivering consistent performance and reducing the risk of human errors. This is the reason why industrial robots are widely used at repetitive and physically demanding tasks. Industrial robots will therefore continue to play a significant role in the output and productivity of future factories.
In recent years, collaborative robots (co-bots) have also emerged as an effective and human-centric alternative to traditional industrial robots for certain tasks. Co-bots are designed to work alongside human operators in shared workspaces, which enables safe and seamless collaboration between humans and robots. Co-bots are typically equipped with advanced sensors and security features to ensure worker safety. Moreover, they can be easily reprogrammed for different tasks, which makes them highly flexible and versatile. Co-bots are used in a variety of manufacturing tasks including machine tending, pick and place, quality inspection, assembly, and packaging.
Note that collaborative robots are typically more affordable than fully-automated industrial robots. This is because they require less complex infrastructure and can be easily integrated into existing production lines, which reduces the cost of implementation and operation. Furthermore, the collaborative approach of co-bots enhances worker acceptance towards automation, as it allows human workers to focus on higher-value tasks while the robots handle repetitive or physically demanding tasks. As already outlined, collaborative robots are also highly flexible and adaptable. They can be quickly reprogrammed to perform different tasks or work in various environments, which enables manufacturers to respond to changing production needs. The benefits will drive an increased adoption and deployment of co-bots in the factories of the future.
Extended Reality and the Industrial Metaverse
Future factories will offer to industrial workers advanced ergonomic user interfaces and immersive experiences, beyond conventional dashboards and visualisations. The development and deployment of immersive experiences in future factories will be based on Virtual Reality (VR), Augmented Reality (AR), and Mixed Reality (MR) technologies, which will gradually be deployed to offer immersive interfaces that enhance safety and productivity.
VR enables users to be fully immersed in a computer-generated environment, blocking out the real world. In essence,VR applications are realistic simulated environments without distracting elements of the real world. By using VR headsets, users can interact with virtual objects and simulate various manufacturing scenarios. Nowadays, VR is notably used for industrial training. For instance, automotive manufacturers utilize VR to simulate assembly line procedures. The latter allow workers to practice complex tasks (e.g., engine installation) in a virtual environment. This type of training enhances efficiency, reduces errors, and minimizes the risk of damaging expensive equipment.
AR overlays digital content onto the real world, seamlessly blending virtual objects with the physical environment. AR can be experienced through smartphones, tablets, or specialized AR glasses. AR deployments in manufacturing are currently used for remote maintenance scenarios. These scenarios involve technicians wearing AR glasses that receive real-time guidance and visualizations, which are superimposed onto the machinery they are working on. For example, in the aerospace industry, AR is used to assist technicians during complex maintenance tasks, displaying step-by-step instructions, diagrams, and highlighting critical components.
MR combines elements of both VR and AR, enabling users to interact with virtual objects that are anchored to the physical world. MR is often achieved through dedicated headsets. In manufacturing, MR offers support to workers by overlaying digital information directly onto their field of view. For instance, warehouse workers use MR headsets to receive real-time pick-and-pack instructions, optimizing order fulfillment processes while minimizing errors.
As outlined in the above-listed examples, the immersive nature of VR, AR, and MR makes them valuable tools for industrial training. Moreover, VR, AR, and MR also play an important role in remote maintenance scenarios. Most importantly, workers can benefit from the on-demand information and support provided by these immersive technologies. Specifically, they can augment the worker's capabilities by overlaying instructions, safety guidelines, or real-time data, which ensures accurate and efficient task execution.
In the scope of the future factories, these technologies will be combined, integrated, and deployed in the industrial metaverse. The latter takes immersive technologies a step further by creating a digital twin of the physical manufacturing environment. It incorporates real-time data, advanced simulations, and predictive analytics to drive simulations and advanced what-if analysis. For instance, manufacturers will use the Industrial Metaverse to simulate production line optimizations, test the impact of process changes, or evaluate alternative workplace layouts.
Industrial Data Spaces
The need for Data Sovereignty and Federated Data Management
As discussed in the previous chapter, future factories will be part of industrial value chains, including circular manufacturing chains. In the scope of such chains, the exchange and utilization of data will be very important. However, such exchange is associated with many security, trust, and data management challenges. One of the main challenges relates to data sovereignty. Data sovereignty refers to the concept of organizations and individuals retaining ownership and control over their own data. In the manufacturing sector, data generated by various actors such as suppliers, manufacturers, circular actors, and customers contains valuable insights that can enhance operational efficiency, innovation, and decision-making. However, concerns relating to privacy, intellectual property, and compliance have brought forward the demand for maintaining data sovereignty. Industrial data spaces address these concerns by providing a framework that allows for secure data exchange while preserving control over data ownership.
One of the most fundamental concepts behind data spaces is federated data management. It involves the decentralized organization and control of data, which allows manufacturing chain actors to retain sovereignty over their own data while enabling secure data sharing and collaboration. Industrial data spaces utilize distributed ledger technologies (like blockchain infrastructures) and advanced data management techniques to establish trust, ensure data integrity, and provide fine-grained access control. Through federated data management, manufacturing chain actors can securely exchange data with trusted partners, in ways that facilitate interoperability, transparency, and innovation.
Common Elements of a Manufacturing Data Space
Some of the most prominent elements and characteristics of a data space infrastructure include:
Data Governance and Policies: Data governance forms the foundation of a manufacturing data space. It defines and enforces data management policies towards data integrity, security, and compliance. Manufacturers establish guidelines for data access control, data ownership, privacy, and consent within a data space. Based on such guidelines they safeguard data sovereignty and encourage secure and trusted data exchange for collaboration across the manufacturing value chain.
Connectivity and Interoperability: Connectivity and interoperability are essential for facilitating seamless data exchange within a manufacturing data space. They are empowered by standardized data formats, protocols, and APIs, which allow for efficient data communication and integration across various systems, machines, and devices. Moreover, open standards (e.g., OPC-UA, MTConnect, CoAP) enable interoperability between machines, sensors, and data management systems, in ways that ensure consistent and reliable data sharing within the data space.
Data Storage and Management: As already discussed in the Big Data section, manufacturers utilize data lakes, data warehouses, and cloud-based storage solutions to accommodate the vast volumes of data generated by connected devices, sensors, and systems. Moreover, advanced data management technologies (e.g., data virtualization, federated data architectures) boost the efficient organization, search, retrieval, and processing of the data.
Security and Privacy: Protective measures like authentication, encryption, and access control mechanisms safeguard data within a data space from unauthorized access. Also, secure identity and access management (IAM) frameworks are used to establish granular control over data sharing and to enforce compliance with privacy regulations such as the General Data Protection Regulation (GDPR) in Europe. As outlined in the blockchain section of this chapter, blockchain technology can be also used to further enhance security, auditability, and data integrity within the data space ecosystem.
Analytics and Data Services: Analytics and data services form an integral part of a manufacturing data space. They empower manufacturers to extract valuable insights from their data. Manufacturers leverage the analytics capabilities of a data space to optimize production processes, improve product quality, and enhance overall operational efficiency.
Manufacturing Data Spaces Use Cases
There are several manufacturing use cases that require the implementation of industrial data spaces. For example, in predictive maintenance, where Original Equipment Manufacturers (OEMs) can securely share real-time sensor data with maintenance service providers. This collaboration enables proactive maintenance actions. Another use case concerns supply chain optimization, where manufacturers can securely exchange production and inventory data with suppliers towards seamless coordination and responsiveness. The integration of data spaces into these use cases enables manufacturers to leverage the collective intelligence of the manufacturing ecosystem, while at the same time maintaining control over their data.
Overall, future factories will be interconnected in supply chains that will leverage federated data management approaches. In this context industrial data spaces will preserve the ownership and control of data, while enabling secure and collaborative data exchange. With data sovereignty at the forefront, manufacturers will unleash the potential of data-driven innovation and digital transformation across interconnected supply chains and circular chains.
Blockchain Technology for Manufacturing Use Cases
The Properties of a Blockchain Network
In recent years blockchain technology has enabled new decentralized approaches to sharing, validating and securing information across the manufacturing value chain. In principle, blockchain is an innovative distributed ledger technology that enables secure and decentralized transactions. Its decentralized nature eliminates the need for intermediaries that oversee processing and validating the different transactions. Rather blockchains establish a peer-to-peer network of participants, which ensures that no single entity has control over the entire system. This enhances resilience, as it eliminates risks associated with a single point of failure. At the same time, it promotes transparency as blockchain transactions are visible to the entire networks of participating nodes.
The immutability of a blockchain infrastructure makes it an ideal solution for maintaining an accurate and verifiable record of events. Once a transaction is added to the blockchain, it becomes nearly impossible to alter or delete, which ensures the integrity of the recorded data. In essence, this tamper-proof feature is achieved through cryptographic hash functions that link each block of data to the previous one. Moreover, blockchains employ advanced cryptographic algorithms to secure data and transactions. Each participant in the network has a unique digital signature, enabling identity verification and preventing unauthorized access. At the same time, a series of consensus mechanisms used in blockchain networks guarantee the agreement and validation of transactions, which enhances security and trust.
The above-listed unique properties of a blockchain network make it an ideal technology for secure and trusted data exchange across manufacturing networks, including data sharing in circular manufacturing chains. Furthermore, blockchain infrastructures provide the means for securing and validating transactions inside factories, which gives rise to a rich set of manufacturing use cases.
Blockchain Use Cases in Manufacturing
The most prominent use case of blockchain technology in manufacturing concerns the decentralized, trusted, and transparent exchange of data in manufacturing supply chains. This is because there are many cases where supply chain participants cannot trust a third party. In such cases a decentralized approach to data sharing (i.e., a blockchain based approach) is preferred. Therefore, blockchain infrastructures are very commonly deployed to enable the decentralized sharing of data across manufacturing actors and circular chain actors, such as manufacturers, remanufacturers, recycling enterprises, regulatory authorities and more. In this context, blockchain technology also enables the establishment and maintenance of a transparent and auditable supply chain that records and tracks every step in the supply chain process towards ensuring data provenance and traceability. Such blockchains store secure information about the origin, location, and quality of raw materials, which enables manufacturers to enhance visibility, mitigate risks, and address issues such as products’ counterfeiting or unauthorized substitutions of products.
Another common use case of blockchain technology in manufacturing concerns asset tracking. Managing and tracking assets across complex manufacturing operations can be challenging. Blockchain offers a decentralized and immutable ledger to record the ownership, maintenance history, and movement of assets. This enables manufacturers to efficiently track their assets, reduce loss, improve maintenance processes, and streamline their occupancy and use in the scope of supply chain operations.
Blockchain technology can also enhance automation by enabling decentralized decision-making. In this direction, decentralized application programs (i.e., smart contracts) are developed to automate various manufacturing processes and enable decentralized control and seamless interaction across production units, suppliers, and customers. One of the benefits of a decentralized automation system lie in the absence of single points of failure, which increases the robustness and resilience of production control processes.
Another blockchain use case in manufacturing is the execution of trusted distributed data analytics functions over the vast amounts of manufacturing data that are generated from production lines, machinery, and sensors. Blockchain technology can facilitate the execution of advanced distributed data analytics functions based on trustworthy data, towards identifying process optimizations and making effective data-driven decisions.
Blockchain Types Deployed in Future Factories
Future factories are likely to comprise blockchain infrastructures in support of decentralized data sharing and control use cases. However, when it comes to implementing blockchain technology in manufacturing and supply chain management use cases, a distinction must be made between permissioned and public blockchains. While public blockchains that support blockbuster cryptocurrencies (e.g., Bitcoin and Ethereum) are well-known for their decentralized and open nature, permissioned blockchains are more suitable for the manufacturing domain.
Contrary to public blockchains that allow anyone with access to the network to view and validate transactions, permissioned blockchains restrict access to a group of trusted participants. This is important for safeguarding the required confidentiality of manufacturing and supply chain processes that use blockchain networks. Most importantly, permissioned blockchains provide much better scalability and performance in terms of the number of transactions per second that they support. This is because permissioned blockchains do not need to implement computationally expensive mining processes and consensus mechanisms but can rather dispose with more lightweight blockchain protocols. Specifically, it is possible for permissioned blockchain networks to support thousands of transactions per second, which is a significant performance boost when compared to public blockchains that require many seconds or even minutes to add a new transaction block to a blockchain network.
Note also that manufacturing and supply chain management are subject to numerous regulations and compliance requirements. Public blockchains operate independently of any centralized authority, which may pose challenges when it comes to aligning with these regulations. The lack of control over the network and the inability to enforce legal or industry-specific requirements can deter manufacturers and supply chain stakeholders from adopting public blockchains. Permissioned blockchains, in contrast, provide a framework where compliance can be embedded into the system's architecture. It is possible to define the rules and regulations within the blockchain's design in order to ensure that production operations and transactions remain fully compliant with applicable laws and regulations.
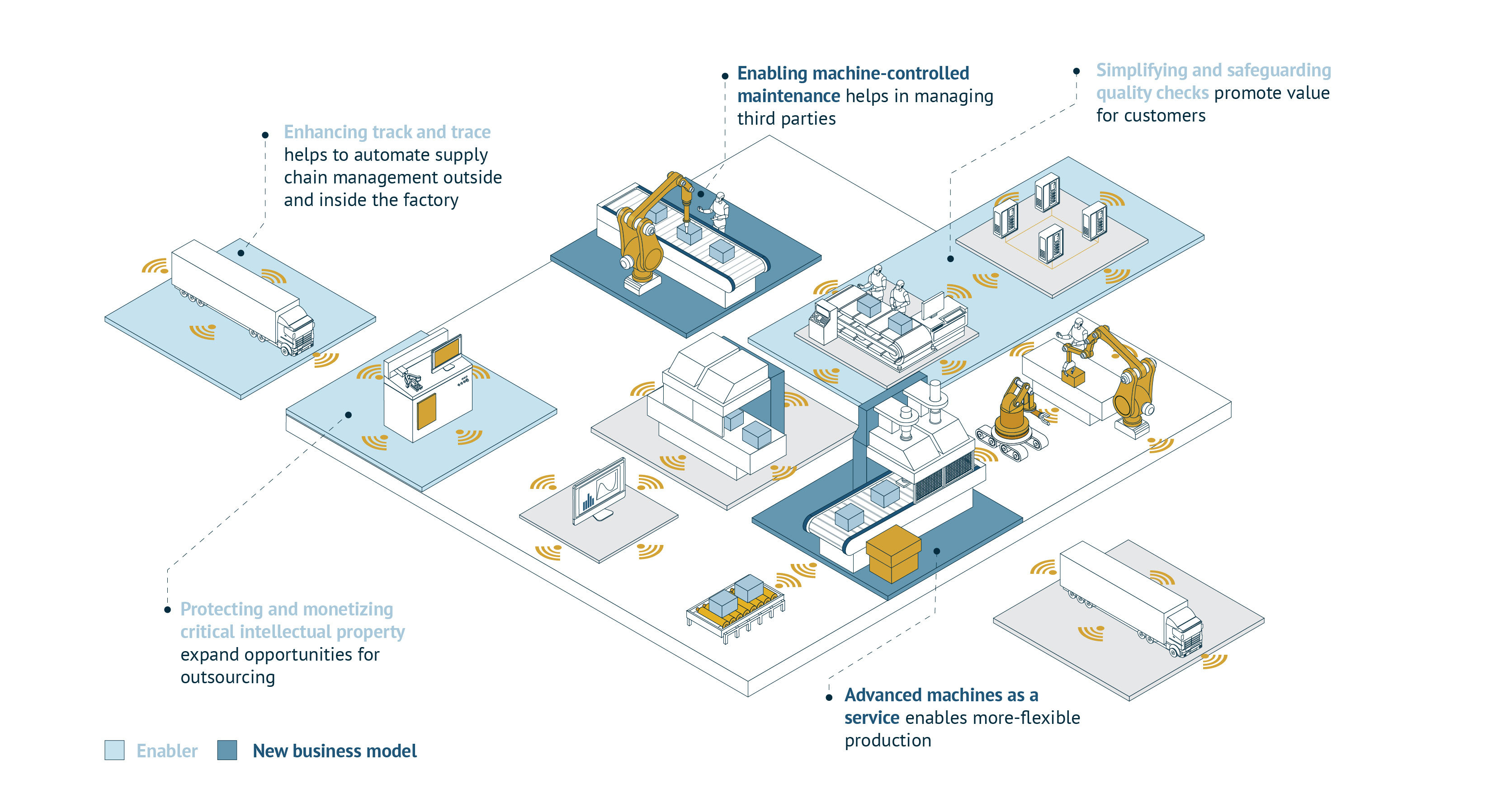
Overall, future factories will be able to leverage the benefits of blockchain technology within a controlled and permissioned network. This will enable manufacturers and supply chain stakeholders to unlock and fully leverage the transparency, security, and data integrity benefits of blockchain infrastructures, without compromising the industrial performance and regulatory compliance.
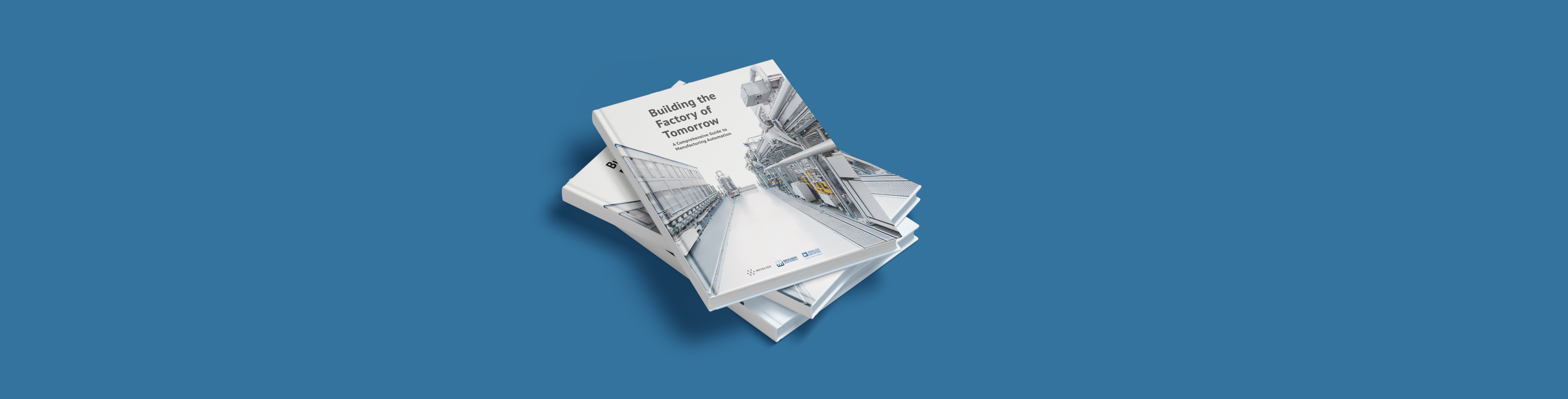