Producing a Drone with Metal 3D Printing
Leveraging metal 3D printing and generative design, this drone project showcases the potential for lightweight, complex structures optimized for performance and manufacturability.
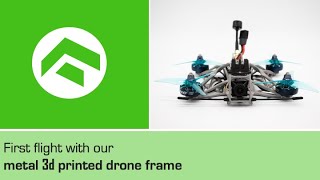
First flight of the printed drone
Metal 3D printing has long been synonymous with industrial applications, powering advancements in sectors like aerospace, automotive, and medical engineering. But its scope reaches far beyond heavy-duty components. A prime example is the drone frame project by designer Till Blaser, which leverages metal additive manufacturing and generative design to create a lightweight, complex, and functional drone frame. This project illustrates the technical possibilities for engineers when combining cutting-edge design software with metal 3D printing technologies.
The Engineering Challenge: Designing a Lightweight, Structurally Sound Drone Frame
The drone project centered around a key challenge: developing a drone frame that minimized weight without sacrificing structural integrity. Traditional methods would have been impractical due to the frame’s complex geometry and the demand for rapid prototyping. The design needed to withstand the stresses of flight, optimize battery life, and support payload capacity—all within stringent weight constraints.
The Solution: Generative Design Meets Metal Additive Manufacturing
To meet these goals, Blaser utilized Autodesk Fusion 360’s generative design capabilities, which allowed him to explore various optimized design iterations based on strength, material usage, and aerodynamics. The result was a highly optimized, bionic structure that would be near-impossible to manufacture conventionally.
The frame was manufactured using Laser Powder Bed Fusion technology, which employed a One Click Metal printer with 200W fiber laser to fuse fine layers of metal powder with exceptional precision. StrengthAl, a high-performance aluminum alloy, was selected due to its excellent strength-to-weight ratio, providing structural robustness with minimal mass. The final frame weighed only 59 grams yet maintained strength properties comparable to titanium—a key achievement for the drone’s performance.
Technical Advantages of Metal 3D Printing for This Project
Weight Reduction: By using StrengthAl and generative design, the frame was optimized for minimal mass without compromising strength. At 59 grams, it allowed for superior flight efficiency and agility, reducing energy consumption during operation.
Complex Geometries and Design Freedom: Metal 3D printing unlocked geometric freedom that is impossible with traditional methods. The frame’s intricate, bionic design was printed as a single unit, eliminating the need for joints or fasteners, which are often weak points in assemblies.
Fast Development Cycles: One of the standout benefits was the rapid iteration cycle. Generative design coupled with metal AM enabled quick adjustments and testing. The entire build process, which involved printing three drone frames simultaneously, was completed in just 36 hours. This reduced time-to-market significantly compared to traditional prototyping processes.
Precision and Surface Quality: LPBF ensured that even the most delicate design features were reproduced with high precision. Post-processing steps such as support removal and sandblasting not only improved the frame’s surface finish but also contributed to its aesthetic appeal without compromising structural function.
The Role of Post-Processing
Post-printing, the drone frame underwent several steps to refine its final appearance and performance. Support structures were carefully removed, and sandblasting was applied to smooth out the surface, improving both aesthetics and functionality. This step is crucial for aerospace-like applications where surface quality can affect aerodynamic performance.
Expanding the Use of Metal 3D Printing
This project serves as a strong case for the potential of metal 3D printing in more consumer-focused designs. By combining Autodesk Fusion 360 and advanced metal AM, the drone frame demonstrated how generative design and metal 3D printing can deliver highly efficient, functional, and visually appealing products quickly. The speed and flexibility provided by this technology open up new avenues for engineers to create components that meet strict performance standards while also pushing the boundaries of design.