Comparing the Contrasts: Lead Based vs. Lead-Free Solder
Unraveling the Soldering Conundrum: A Thorough Analysis of Lead and Lead-Free Solder, Their Effects on Electronics Manufacturing, Health, the Environment, and Practical Insights for Informed Decision-Making
Soldering on circuit board with soldering iron and solder in board repairing
Introduction
Soldering, a fundamental process in the realm of electronics, plays a pivotal role in the assembly and maintenance of electronic devices. This technique involves the utilization of a filler material, known as solder, to conjoin metal surfaces. The solder is subjected to heat until it reaches its melting point and seamlessly integrates into the joint between the two surfaces. Upon cooling, it solidifies, establishing a robust electrical and mechanical connection.
Within the electronics industry, two primary types of solder take center stage: lead-based solder and lead-free solder. Lead-based solder has enjoyed widespread usage for several years primarily owing to its exceptional performance characteristics. Nevertheless, driven by health and environmental apprehensions linked to that, there has been a significant shift towards the use of lead-free solder in recent years. Gaining a profound understanding of the distinctions between these two types proves paramount for all stakeholders in the field of electronics, as it profoundly influences the quality of solder joints, and the performance of electronic devices, and the safety of individuals engaging in soldering activities.
The Composition of Solder
Solder, a fusible metal alloy employed to establish a durable bond between metal workpieces, exhibits a composition that can significantly vary depending on its designated application. is a fusible metal alloy used to create a permanent bond between metal workpieces. Typically, solder comprises a blend of metals, including tin, lead, silver, and copper. Each of these elements contributes to the overall properties of the solder, affecting factors such as its melting point, strength, and electrical conductivity.
Tin frequently serves as a principal solder due to is relatively low melting point and excellent wetting properties., These properties enable it to effortlessly spread across the surfaces to be joined, ensuring effective bonding. Copper and silver are sometimes added to enhance the mechanical strength and electrical conductivity of the solder. Moreover, elements such as antimony may be introduced to bolster the solder’s resistance to mechanical fatigue, a critical consideration in electronic applications.
Recommended Readings: A Practical Guide to Solder Flux
Lead-Based Solder
Lead-based solder, known as tin-lead (Sn-Pb) solder, stands as the historical cornerstone of the electronics industry. The most prevalent formulation, a 60/40 blend of 60% tin and 40% lead, remains a staple choice. Understanding the technical nuances of this solder alloy is essential for engineers and technicians in the field.
Composition and Melting Point
The specific composition of a solder alloy greatly influences its characteristics. In the case of 60/40 lead-based solder, it exhibits:
- Tin (Sn): 60%
- Lead (Pb): 40%
One of the standout features of this alloy is its relatively low melting point, which stands at 188°C. This low melting point is a significant advantage as it minimizes the heat required for the solder to transition into its liquid form and flow smoothly into joints.
The presence of lead in the solder also contributes to its excellent performance characteristics. Lead lowers the melting point of the solder, improves its wetting properties, and reduces the formation of tin whiskers - a phenomenon where conductive, crystalline structures of tin grow from the surface of the solder over time, which can lead to electrical shorts.
Metal silver base smelting blank, lead ballMelting Point Equations
To quantify this effect, we can use the relationship between temperature (T), melting point (Tm), and alloy composition in the form of a linear equation:
T=Tm −kC
Where:
- T is the alloy's melting point.
- Tm is the melting point of the pure metal (e.g., tin or lead).
- k is a constant.
- C represents the concentration of the element in the alloy.
Strength and Electrical Conductivity
Aside from its melting point, the inclusion of lead in the solder is instrumental in enhancing mechanical strength and electrical conductivity. This is particularly vital in electronic applications where soldered connections must endure mechanical stress and ensure efficient current flow.
Melting point comparison
Property 60/40 Lead-Based Solder Melting Point (°C)
--------------------------------------------------------------------------------------
Melting Point (°C) 188 Varies
--------------------------------------------------------------------------------------
Mechanical Strength Enhanced Application-specific
--------------------------------------------------------------------------------------
Electrical Conductivity Enhanced Application-specific
--------------------------------------------------------------------------------------
Tin Whisker Formation
One of the critical issues addressed by lead-based solder is the formation of tin whiskers. These conductive, crystalline structures emerge from the solder's surface over time. Tin whiskers can pose a significant risk of electrical shorts in electronic circuits. The presence of lead in the solder effectively mitigates tin whisker formation, ensuring long-term reliability.
Despite its merits, lead-based solder has seen a decline in usage. This transition is driven by concerns related to human health risks associated with lead exposure and environmental considerations, primarily to align with regulations like the Restriction of Hazardous Substances Directive (RoHS) within the European Union.
Lead-Free Alternatives
The shift towards lead-free solder alternatives has introduced a new era in electronics manufacturing. These alloys offer a range of compositions with varied properties to cater to specific applications. For instance, lead-free solder alternatives like tin-silver-copper (Sn-Ag-Cu) solder are widely adopted due to their environmental compliance and robust mechanical and electrical properties.
Lead-Free Solder
Lead-free solder represents a significant stride in the electronics industry, championing safety for both individuals and the environment. This solder variety, as its name implies, entirely lacks lead, addressing critical health and ecological concerns. Let's delve into the composition and properties of lead-free solder, particularly beneficial for engineering graduates and practitioners.
Soldering on circuit board with soldering iron and solder in board repairingComposition and Diverse Blends
The composition of lead-free solder varies, with tin frequently playing a dominant role, often exceeding 95% of the alloy's makeup. Additional elements such as copper, silver, and occasionally bismuth or antimony are skillfully integrated to augment the solder's performance attributes.
Common Lead-Free Solder Compositions
Solder Type Tin (Sn) Copper (Cu) Silver (Ag)
------------------------------------------------------------------------------------------
Tin-Copper (Sn-Cu) 99.3% 0.7%- -
------------------------------------------------------------------------------------------
Tin-Silver-Copper (SAC) 96.5% 0.5% 3%
------------------------------------------------------------------------------------------
Melting Points and Equations
The melting point of lead-free solder alloys, such as Sn-Cu and SAC, varies from traditional lead-based solder. Let's quantify this difference with an equation:
TLF =Tm+kC
Where:
- TLF is the melting point of the lead-free solder.
- Tm is the melting point of the pure metal (e.g., tin).
- k is a constant.
- C represents the concentration of the element in the alloy.
For example, the tin-copper (Sn-Cu) solder boasts a higher melting point, typically around 227°C. This elevated melting point offers stronger solder joints once cooled, ideal for applications that demand robust mechanical connections.
Advantages and Challenges
Lead-free solder exhibits distinct advantages, but it's not without challenges. For instance, it tends to be less ductile than lead-based solder, rendering it more susceptible to mechanical stress. Moreover, lead-free solder tends to oxidize more rapidly, which can adversely affect its wetting properties and solder joint quality.
Solder engineers and technicians can effectively address these challenges through meticulous handling and precise process control. Proper flux selection and techniques are vital to mitigate oxidation and achieve high-quality solder joints in lead-free assemblies.
Recommended Readings: Lead vs. Lead-free Solder: Which is better for PCB manufacturing?
The Soldering Process
Soldering is a process that involves the use of a filler material, known as solder, to join together metal surfaces. The solder is heated until it melts and flows into the joint between the two surfaces. Upon cooling, it hardens and forms a reliable electrical and mechanical connection.
Basic Principles and Variations
The basic principles of soldering remain consistent, irrespective of the specific soldering method employed. Whether it's surface-mount soldering, through-hole soldering, or other variants, the core concept involves meticulously controlling the transition of solder to create a strong bond between metal surfaces.
Surface Preparation
The soldering process begins with the preparation of the surfaces to be joined. This typically involves cleaning the surfaces to remove any oxidation or contaminants that could interfere with the formation of a good solder joint.
Soldering a board, using electronics and modern technologiesSolder Application
Once the surfaces are prepared, the solder is applied to the joint. This is usually done by heating the solder with a soldering iron until it melts and flows into the joint.
Influence of Solder Composition
The composition of the solder plays a crucial role in the soldering process. Different types of solder have different melting points, wetting properties, and mechanical characteristics, all of which can affect the ease of soldering and the quality of the resulting solder joint.
Soldering with Lead-Based Solder
Soldering with lead-based solder is often considered easier than soldering with lead-free solder due to its lower melting point and superior wetting properties. The lower melting point of lead-based solder means that it requires less heat to melt and flow into the joint, which can make the soldering process quicker and less likely to damage heat-sensitive components.
Lower Melting Point Advantage
One of the distinctive attributes of lead-based solder is its lower melting point. This characteristic reduces the heat required for the solder to transition into its liquid state and flow into the joint. The lower melting point not only expedites the soldering process but also minimizes the risk of damaging heat-sensitive components, a crucial consideration in the electronics industry.
Superior Wetting Properties
Lead-based solder further distinguishes itself with superior wetting properties. Wetting refers to the ease with which solder spreads across the surfaces to be joined. The superior wetting capacity of lead-based solder allows it to form a robust electrical and mechanical connection with minimal effort. This property proves especially advantageous when soldering components with intricate geometries, where effective wetting is indispensable for achieving reliable solder joints.
Challenges and Safety Considerations
However, while lead-based solder offers numerous advantages, it does come with notable challenges. The most significant among these is the health risk associated with lead exposure. Lead is a toxic metal capable of causing severe health issues if inhaled or ingested. As a result, it's imperative to adhere to appropriate safety precautions when soldering with lead-based solder:
- Work in a Well-Ventilated Area: Adequate ventilation helps disperse any potentially harmful fumes generated during the soldering process.
- Use a Fume Extractor: Employ a fume extractor to effectively remove soldering fumes, further reducing the risk of inhaling lead particles.
- Hand Hygiene: After soldering, it's crucial to wash hands thoroughly to prevent any accidental ingestion of lead through hand-to-mouth contact.
Soldering with lead-based solder offers simplicity and efficiency but demands a strong commitment to safety and responsible handling.
Soldering with Lead-Free Solder
Soldering with lead-free solder presents distinct challenges compared to its lead-based counterpart. While it demands greater care and precise technique, it aligns with essential health and environmental considerations. Let's explore the intricacies of soldering with lead-free alternatives.
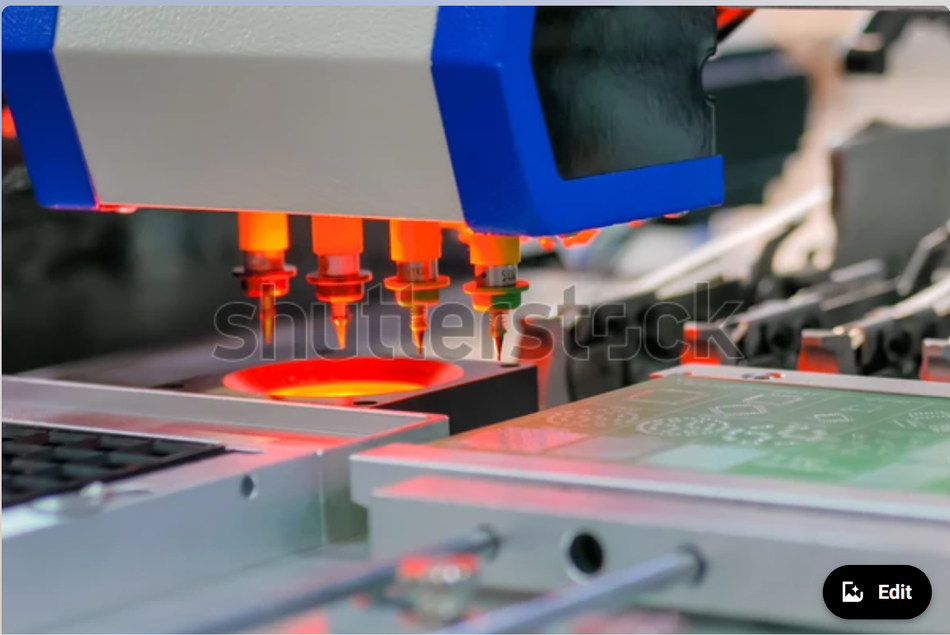
Process of selective soldering components to printed circuit boards at factory.
Higher Melting Point and Careful Management
The most noticeable difference in lead-free soldering is the elevated melting point. Lead-free solder alloys, such as tin-silver-copper (SAC), often require higher temperatures for melting and flowing into joints, demanding a meticulous approach. While this might extend the soldering process, the risk of damaging heat-sensitive components underscores the need for careful management.
Melting Points of Solder Types
Solder Type Melting Point (°C )
--------------------------------------------------------------------------------------
Lead-Based Solder 188 188
--------------------------------------------------------------------------------------
Lead-Free Solder (SAC) 217-220
--------------------------------------------------------------------------------------
Challenges in Wetting Properties
Lead-free solder, due to its unique composition, may exhibit less favorable wetting properties compared to lead-based solder. It may not spread as easily over the surfaces to be joined, posing challenges in achieving effective electrical and mechanical connections. This can be particularly pronounced when soldering components with intricate geometries, where achieving optimal wetting is pivotal for the integrity of the solder joint.
Adapting Techniques and Equipment
To succeed in soldering with lead-free solder, it's vital to adapt your techniques and equipment. Consider the following:
- Soldering Iron: Utilize a soldering iron with a higher temperature range to accommodate the elevated melting point of lead-free solder.
- Process Adjustment: Adjust your soldering process to account for the distinct wetting properties of lead-free solder, ensuring effective adhesion.
- Flux Utilization: Employ a compatible flux to enhance wetting and minimize oxidation. Proper flux selection contributes to successful solder joints.
Selecting the Right Lead-Free Solder
Lead-free solder encompasses a variety of types, each with unique properties and performance characteristics. It's essential to choose the suitable lead-free solder for your specific application. This choice ensures a smooth soldering process and dependable solder joints.
Recommended Readings: SMT Manufacturing: Everything You Need to Know
Performance Comparison: Lead vs Lead-Free Solder
In the realm of soldering, understanding the performance disparities between lead and lead-free solder is crucial. This evaluation encompasses factors such as durability, electrical conductivity, melting point, and the evolving landscape of solder materials.
Durability and Mechanical Resilience: Lead-free solder, by nature, tends to be less ductile compared to its lead-based counterpart. This characteristic renders it more susceptible to mechanical stress, raising concerns regarding solder joint integrity under specific conditions. Vibrations, thermal cycling, and external forces can challenge the durability of lead-free solder joints. However, it's vital to note that innovative lead-free solder alloys, such as the renowned SAC (tin-silver-copper), have been engineered to address this vulnerability. These advanced alloys offer improved mechanical strength, significantly reducing the risk of joint failure.
Enhancing Electrical Conductivity: The electrical conductivity of solder is a pivotal determinant of electronic device performance. Lead-based solder generally enjoys a slight advantage in terms of electrical conductivity, which translates to lower electrical resistance and, in some cases, improved overall device performance. Nevertheless, the variance in electrical conductivity between lead and lead-free solder is typically marginal and is unlikely to significantly affect the majority of electronic applications.
Balancing Melting Point and Solder Joint Strength: Lead-free solder's distinguishing feature is its higher melting point when juxtaposed with lead-based solder. This difference introduces both advantages and challenges. The elevated melting point necessitates a higher soldering temperature, demanding precise temperature control during the soldering process. While this might extend the soldering duration, it rewards engineers with notably stronger solder joints. However, it also introduces a potential concern – the risk of damaging heat-sensitive components during soldering.
Expanding the Perspective: Environmental Impact
Beyond the performance parameters, the choice between lead and lead-free solder is influenced by larger considerations. In recent years, environmental and health factors have profoundly shaped the electronics industry. Lead-based solder, long cherished for its performance, has faced mounting scrutiny due to its environmental impact and potential health hazards. The Restriction of Hazardous Substances (RoHS) directive issued by the European Union has played a pivotal role in phasing out the use of lead-based solder in various applications.
Comprehensive Solder Performance Comparison
Property Lead-Based Solder Lead-Free Solder
--------------------------------------------------------------------------------------------------
Durability Ductile Enhanced with Advanced Alloys
--------------------------------------------------------------------------------------------------
Electrical Conductivity Slightly Higher Marginally Lower
---------------------------------------------------------------------------------------------------
Melting Point Lower Higher
--------------------------------------------------------------------------------------------------
Environmental Impact Challenging Aligned with RoHS Guidelines
--------------------------------------------------------------------------------------------------
In summary, while there are some differences in performance between lead and lead-free solder, both types can be used effectively in a wide range of electronic applications. The choice between the two will largely depend on factors such as the specific requirements of the project, health and safety considerations, and environmental impact.
Health and Environmental Impacts
When choosing the appropriate solder for a project, it's essential to consider the significant health and environmental implications associated with both lead and lead-free solder, particularly in the context of circuit boards, PCBs, and the diverse needs of hobbyists.
Health Risks Associated with Lead-Based Solder: Lead, a toxic metal, poses the potential to cause severe health problems when inhaled or ingested. Exposure to lead can result in neurological damage, kidney dysfunction, and reproductive issues, among other critical health concerns. Workers involved in electronics manufacturing and PCB assembly may be particularly susceptible to lead exposure through inhalation of lead fumes or contact with lead particles during the soldering process. To mitigate these risks, it is paramount to adhere to rigorous safety measures, including:
- Adequate Ventilation: Work in a well-ventilated area to dissipate harmful lead fumes.
- Fume Extraction: Employ a fume extractor to effectively remove soldering fumes from the workspace.
- Hygiene Practices: Thoroughly wash hands after soldering to prevent inadvertent ingestion of lead.
Environmental Impacts of Lead-Based Solder: The environmental impact of lead-based solder extends beyond health concerns, notably in the disposal of electronic devices containing this solder. There is a potential for lead to leach into the environment, contaminating soil and water sources. This contamination can have detrimental consequences for ecosystems and pose a health risk to humans through the consumption of contaminated food or water.
Environmental Impacts of Lead-Free Solder: Lead-free solder, while generally deemed more environmentally friendly than its lead-based counterpart, is not entirely devoid of environmental concerns. The extraction and processing of metals used in lead-free solder, such as tin and silver, can contribute to negative environmental effects, including habitat destruction, water pollution, and increased energy consumption. However, the overall environmental impact of lead-free solder is generally considered to be lower than that of lead-based solder, primarily due to the reduced risk of lead contamination.
Balancing the use of lead or lead-free alloys during PCB manufacturing and assembly, particularly in surface-mount technology (SMT) and stencil-based processes, requires careful consideration. While the eutectic properties of lead-based solder can be advantageous for achieving efficient, defect-free soldering, the health risks associated with lead fumes and the environmental consequences must be weighed against these benefits.
In conclusion, the choice between lead and lead-free solder is a multifaceted decision, especially in the context of PCB assembly, hobbyist projects, and eutectic properties for efficient soldering. Engineers and hobbyists must weigh specific project requirements, health and safety considerations, environmental responsibility, and performance expectations to determine the optimal solder type. Balancing these aspects is crucial in making informed choices for circuit boards, particularly in SMT processes where wettability and reduced environmental impact play a pivotal role.
Recommended Readings: Demystifying Soldering Techniques
Regulations and Industry Standards
The shift from lead-based solder to lead-free alternatives, especially concerning printed circuit boards (PCBs) and capacitors, is underpinned by stringent regulations and intricate industry standards. Engineering graduates need to grasp the depth of these transitions, as they form the backbone of modern electronics manufacturing.
Restriction of Hazardous Substances (RoHS) Directive: The RoHS Directive, enforced by the European Union since 2003, has transformed the landscape of soldering in electronics. It imposes strict limits on hazardous substances, notably lead, which is now restricted to a mere 0.1% by weight. For engineering graduates, this mandates a profound exploration of lead-free soldering techniques. It also necessitates a deeper understanding of the intricate thermal dynamics in reflow soldering, which plays a critical role in creating reliable solder joints on PCBs. The demand for lead-free alloys with higher melting points underscores the importance of scrutinizing the precise composition of solder paste and the solder wire, particularly in applications where capacitors with unique specifications are required. Engineering graduates must navigate the complex terrain of solder wettability to ensure the quality and reliability of solder joints, while also addressing impurities that could undermine performance.
Waste Electrical and Electronic Equipment (WEEE) Directive: The WEEE Directive, in conjunction with RoHS, champions eco-friendliness. It compels engineering graduates to delve into the world of recycling processes and environmentally sustainable materials. Capacitor technology is central to this endeavor, as it aligns with the directive's goals of reducing electronic waste. Graduates must grapple with the selection of capacitors that cater to diverse applications, carefully considering factors such as capacitance, voltage ratings, and temperature coefficients. The transition to lead-free solder, while contributing to environmental conservation, necessitates a closer examination of solder paste compositions, especially those that can function efficiently at lower temperatures.
International Electrotechnical Commission (IEC) Standards: The IEC provides a robust framework for lead-free solder use in electronics manufacturing. Its standards encompass an array of crucial aspects, including solder alloy selection, handling protocols, and best practices for lead-free solder utilization. Engineering graduates must become proficient in deciphering these standards, understanding the intricacies of solder paste formulations, and analyzing the impact of tin content on solder joint quality. They must delve into the world of metal dendrites, microscopic conductive structures that can potentially lead to short circuits and impaired circuit board functionality. The IEC guidelines offer a blueprint for engineering graduates to ensure the quality, performance, and reliability of electronic components in an environment that increasingly demands sustainability and environmental consciousness.
In summary, the regulations and industry standards underpinning the transition from lead-based to lead-free solder in electronics manufacturing are multifaceted and technically demanding. For engineering graduates, this transition involves not only navigating the metallurgy of lead-free solder alloys but also comprehending the intricate thermal profiles required for successful reflow soldering. They must become proficient in the selection of capacitors for a multitude of applications and understand the trade-offs between various capacitor characteristics. Additionally, they must unravel the complexities of solder paste compositions, wettability dynamics, and the implications of impurities on solder joint integrity. A deep dive into metal dendrites and their prevention from causing short circuits rounds out the graduate's holistic knowledge of electronics manufacturing. These standards, while addressing health and environmental concerns, offer a window into the world of cutting-edge soldering methodologies, materials, and quality assurance practices in modern electronics production.
Choosing the Right Solder for Your Project
Selecting the appropriate solder for your project is an important decision that can impact the quality of the soldered joints, the performance of the electronic device, and the health and safety of the individual performing the soldering. Here are some factors to consider when choosing between lead and lead-free solder:
Intended Use and Solder Performance:
- Delve into the specifics of your project's requirements and how they align with solder characteristics.
- High-Temperature Applications and Mechanical Strength: Explore the need for lead-free solder with a higher melting point and superior mechanical properties, like SAC solder.
Prioritizing Health and Safety:
- Focus on safeguarding the health and well-being of those involved in soldering.
- Lead Exposure Concerns: Assess the risks associated with lead and the importance of following safety precautions.
- Proper Ventilation and Fume Extraction: Highlight the significance of working in well-ventilated areas and utilizing fume extractors.
Environmental and Sustainability Impact:
- Weigh the environmental consequences of your project and opt for eco-friendly solder.
- Comparing Environmental Concerns: Address the trade-offs between lead-based and lead-free solder in terms of environmental impact.
- Reducing the Risk of Lead Contamination: Discuss the benefits of lead-free solder in minimizing the risk of lead pollution.
Navigating Regulations and Industry Standards:
- Understand the regulatory landscape and industry standards shaping solder selection.
- RoHS Directive Compliance: Explore the implications of the RoHS Directive, particularly regarding the restricted use of lead in solder.
- IEC Standards: Explain how International Electrotechnical Commission standards play a crucial role in guiding solder selection.
Equipment and Technique Adaptations
- Recognize the need for adjustments when transitioning from lead-based to lead-free solder.
- Soldering Iron and Temperature Considerations: Detail the importance of choosing the right soldering iron and temperature range.
- Wetting Properties and Flux: Highlight how differences in wetting properties between lead and lead-free solder necessitate technique adjustments and the use of compatible flux.
By carefully considering these factors and weighing the advantages and disadvantages of lead and lead-free solder, you can make an informed decision about the best solder for your specific project.
Conclusion
In the intricate world of electronics, discerning the nuances between lead and lead-free solder transcends choice; it becomes a necessity. The repercussions touch every facet of the soldering process, from soldered joint quality to electronic device performance and the well-being of those at the soldering helm. Through meticulous evaluation of project requisites, unwavering commitment to health and safety practices, due diligence on environmental impact, and adherence to pertinent regulations and industry standards, a well-informed solder selection emerges. As the electronics industry continually adapts to evolving regulations and environmental imperatives, the pursuit of knowledge in soldering technology and best practices remains an unwavering path forward. It's in these considerations that the harmonious symphony of soldering reaches its zenith, resonating with the promise of a better, safer, and more sustainable electronic future.
References
- Comparisons of Mechanical Properties of sub-mm Lead Based and Lead Free Based Solder Using in Manufacturing of Printed Circuits
- A review of lead-free solders for electronics applications
- Mechanical properties of a lead-free solder alloys
- Are you ready for lead-free electronics?
- Overview of lead-free solder issues including selection
Frequently Asked Questions
What are the main differences between lead and lead-free solder?
The primary differences include composition, melting points, environmental impact, and health concerns. Lead-free solder contains metals like tin, copper, and silver, has a higher melting point, and is considered more environmentally friendly. Lead-based solder contains lead, has a lower melting point, but raises health and environmental concerns due to lead toxicity.
Why is lead-free solder becoming more popular?
Lead-free solder is gaining popularity due to health and environmental concerns associated with lead-based solder. It meets regulatory requirements, reduces the risk of lead contamination, and aligns with eco-friendly practices.
Can I use lead-free solder with my existing soldering equipment?
Yes, you can use lead-free solder with existing equipment, but it may require adjustments. Lead-free solder has a higher melting point, so you might need a soldering iron with a broader temperature range. Additionally, consider using a compatible flux to enhance wetting and reduce oxidation.
How do I choose the right solder for my project?
A: Selecting the right solder involves assessing your project's requirements, considering health and safety aspects, evaluating environmental concerns, adhering to relevant regulations, and adjusting soldering equipment and techniques as needed for lead-free solder.
Table of Contents
IntroductionThe Composition of SolderLead-Based SolderComposition and Melting PointMetal silver base smelting blank, lead ballMelting Point EquationsStrength and Electrical ConductivityMelting point comparison Tin Whisker FormationLead-Free AlternativesLead-Free SolderSoldering on circuit board with soldering iron and solder in board repairingComposition and Diverse BlendsCommon Lead-Free Solder CompositionsMelting Points and EquationsAdvantages and ChallengesThe Soldering ProcessBasic Principles and VariationsSurface PreparationSoldering a board, using electronics and modern technologiesSolder ApplicationInfluence of Solder CompositionSoldering with Lead-Based SolderLower Melting Point AdvantageSuperior Wetting PropertiesChallenges and Safety ConsiderationsSoldering with Lead-Free SolderProcess of selective soldering components to printed circuit boards at factory.Higher Melting Point and Careful ManagementMelting Points of Solder TypesChallenges in Wetting PropertiesAdapting Techniques and EquipmentSelecting the Right Lead-Free SolderPerformance Comparison: Lead vs Lead-Free SolderExpanding the Perspective: Environmental ImpactComprehensive Solder Performance ComparisonHealth and Environmental ImpactsRegulations and Industry StandardsChoosing the Right Solder for Your ProjectIntended Use and Solder Performance:Prioritizing Health and Safety:Environmental and Sustainability Impact:Navigating Regulations and Industry Standards:Equipment and Technique AdaptationsConclusionReferencesFrequently Asked Questions